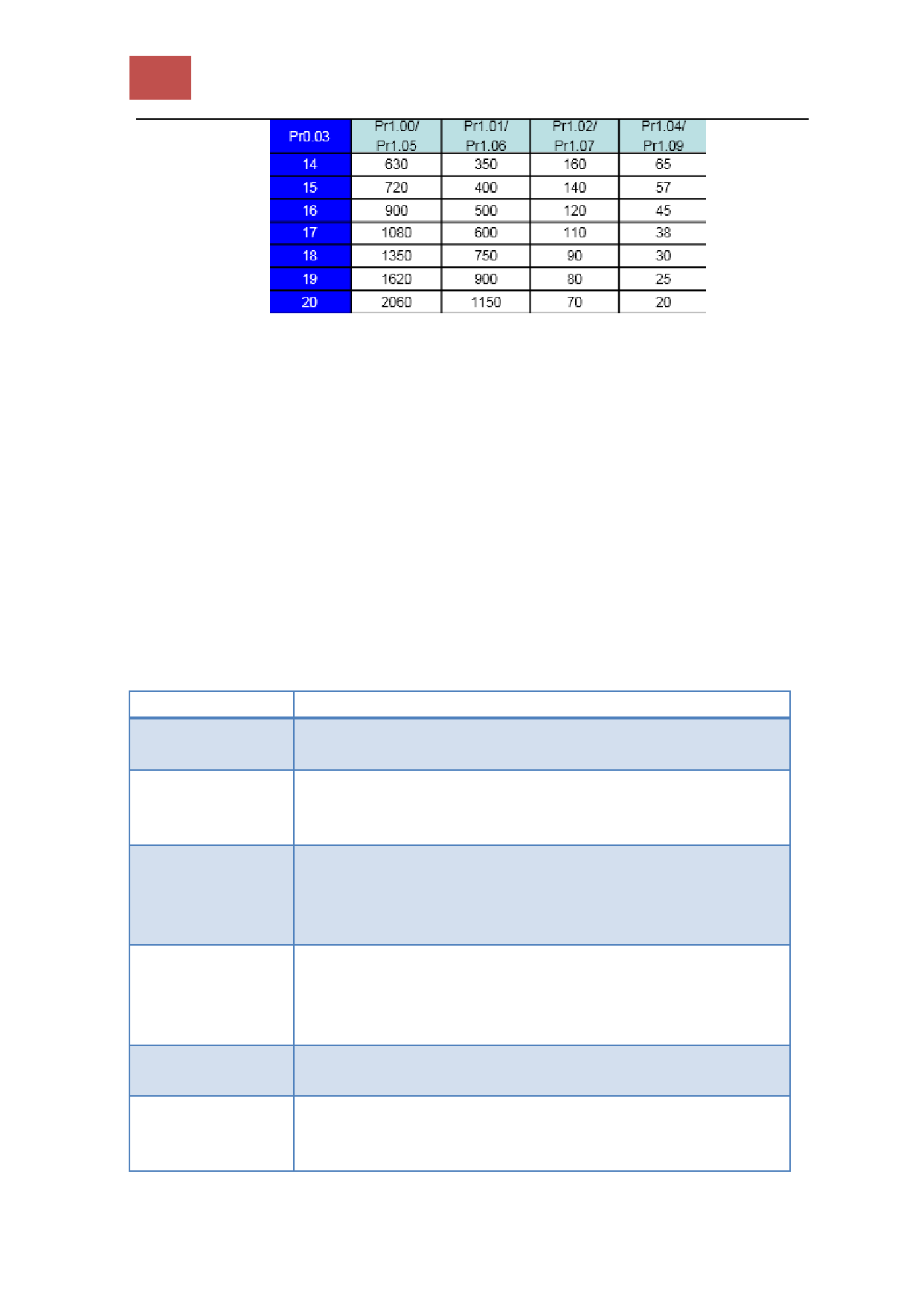
55 FSCUT2000C laser cutting control system User Manual
5.2.4 DELTA servo debugging experience
Delta servo debugging can also refer to the rigidity table of Panasonic. The
reference method is shown as below:
The parameter P2-00 KPP is the equal of the position loop gain of Panasonic.
Though its unit is rad/s, actually, It's 1/s. For example, when the P2-00 KPP= 90, it’s
the same as Pr100=900 of the position loop gain of Panasonic.
5.3 Motion Control parameter adjustment
5.3.1 Motion control parameter introduction
FSCUT2000C system mainly opens these four types of motion control
parameters, such as speed, acceleration, FIR frequency, corner and circular accuracy,
to users to adjust. Other sports-related parameters have been optimized internally
without needing user settings. The meanings of these four parameters are shown as
below:
Name
Move speed
Move acceleration
Max acceleration
FIR frequency
Circle precision
Corner precision
Introduction
Maximum speed of air moving, can be directly fill with
the maximum move speed calculated by Servo Tools software.
Maximum acceleration of air moving, can be directly fill with
the maximum move acceleration calculated by Servo Tools
software.
Maximum acceleration during processing, directly determines
the time of acceleration and deceleration of the turning
movement during cutting. Adjust by observing the torque curve
of servo.
Suppress filter frequency of machine vibration. The smaller the
value is, the more obvious the effect of suppressing the
vibration is, but which will make the time of acceleration and
deceleration longer
Arc accuracy limit. The lower the value of the arc precision, the
more obvious the limit of arc speed is.
Fit with corner precision by NURBS curve. The lower the value
is, the closer the corner is closed to sharp corner, but the
deceleration will be more significant.