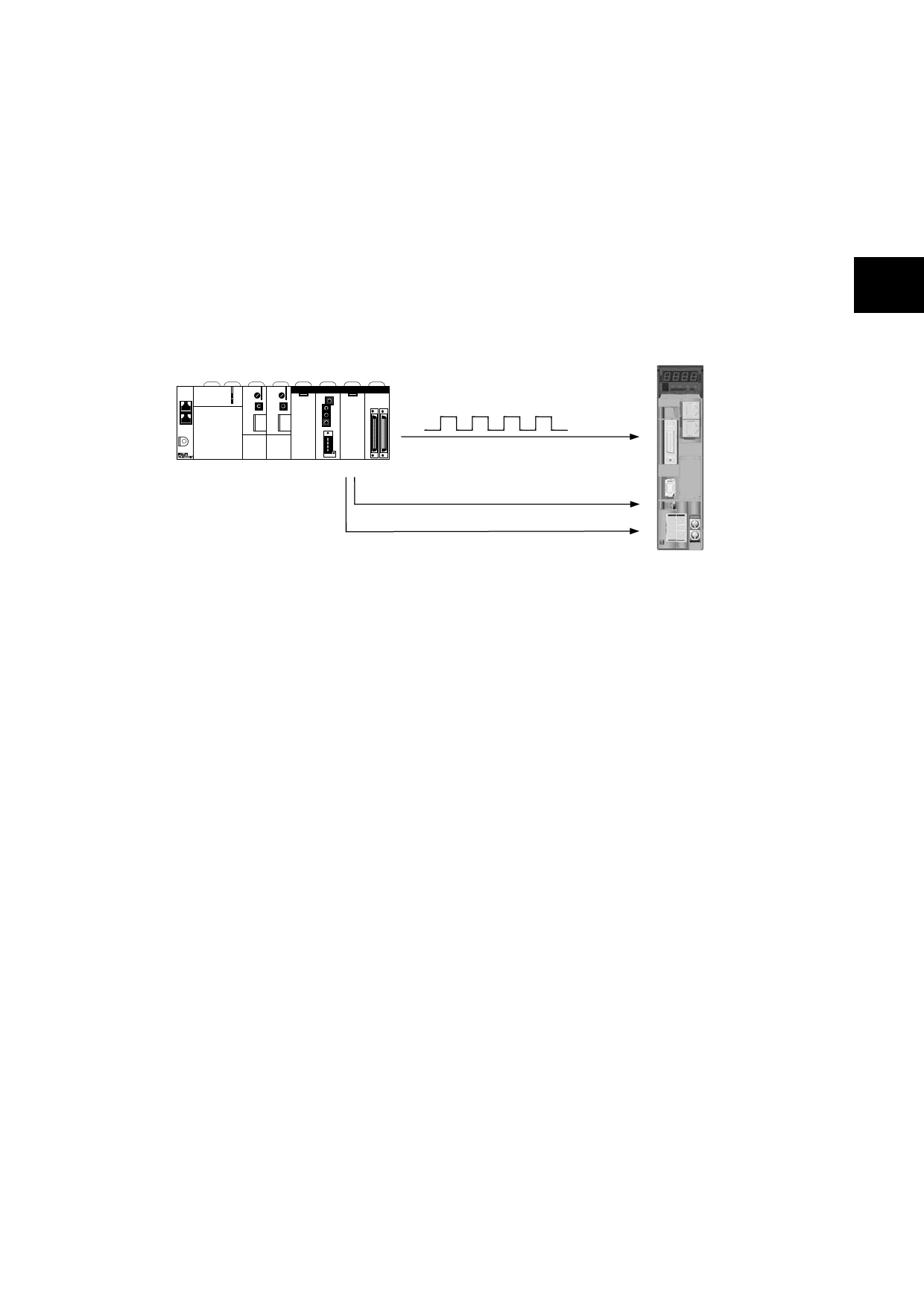
CHAPTER 2 WIRING
Parameter setting
To assign position control to a sequence input terminal, specify the corresponding value ("37") to
the input terminal function setting parameter. For command pulse ratio 1, specify ("27"), while
specify ("28") for command pulse ratio 2.
[Example] To conduct operation with a command pulse input
Operation with a command pulse input is enabled while command pulse ratio 1 or
command pulse ratio 2 remains turned on after the position control signal is turned
2
on.
APS30
SX
SCPU3
SCPU3
ONL 0 1 2 3 4 5 6 7
ONL
2
RUN
ONL
ERR
TERM
2
RUN
ONL
ERR
ERR 8 9 101112131415
ERR
TERM
PWR
SLV
RUN
SLV
RUN
ALM
ALM
STOP
BAT
STOP
BAT
CH
ALM
No.
CPU
CPU
No.
No.
PH
PL
LOADER
LOADER
DA
ONL 0 1 2 3 4 5 6 7
ONL
ERR 8 9 101112131415 ERR
CH1
EMG +OT -OT
CH2
20
PE1
1
B/A
HP2
Pulse
Position control (37)
Command pulse ratio 1 (27)
Relevant description
(1) PA1_06: numerator 0 of electronic gear /PA1_07: denominator of electronic gear
In the factory shipment state, each pulse of a pulse input turns the servomotor by 16 encoder
pulses.
With an incremental encoder, each revolution of the motor shaft corresponds to 1048576 pulses
(20 bits).
Use the electronic gear to change the rotation amount of the servomotor corresponding to each
pulse of the pulse input.
(2) PA2_54: command pulse ratio 1/PA2_55: command pulse ratio 2
Numerator 0 of electronic gear and denominator of electronic gear convert the traveling amount of
the mechanical system per each pulse of the pulse input into a unit amount.
Or the multiplication of the traveling amount of the mechanical system can be changed with
command pulse ratio 1 or command pulse ratio 2.
Description of I/O Signals 2-45