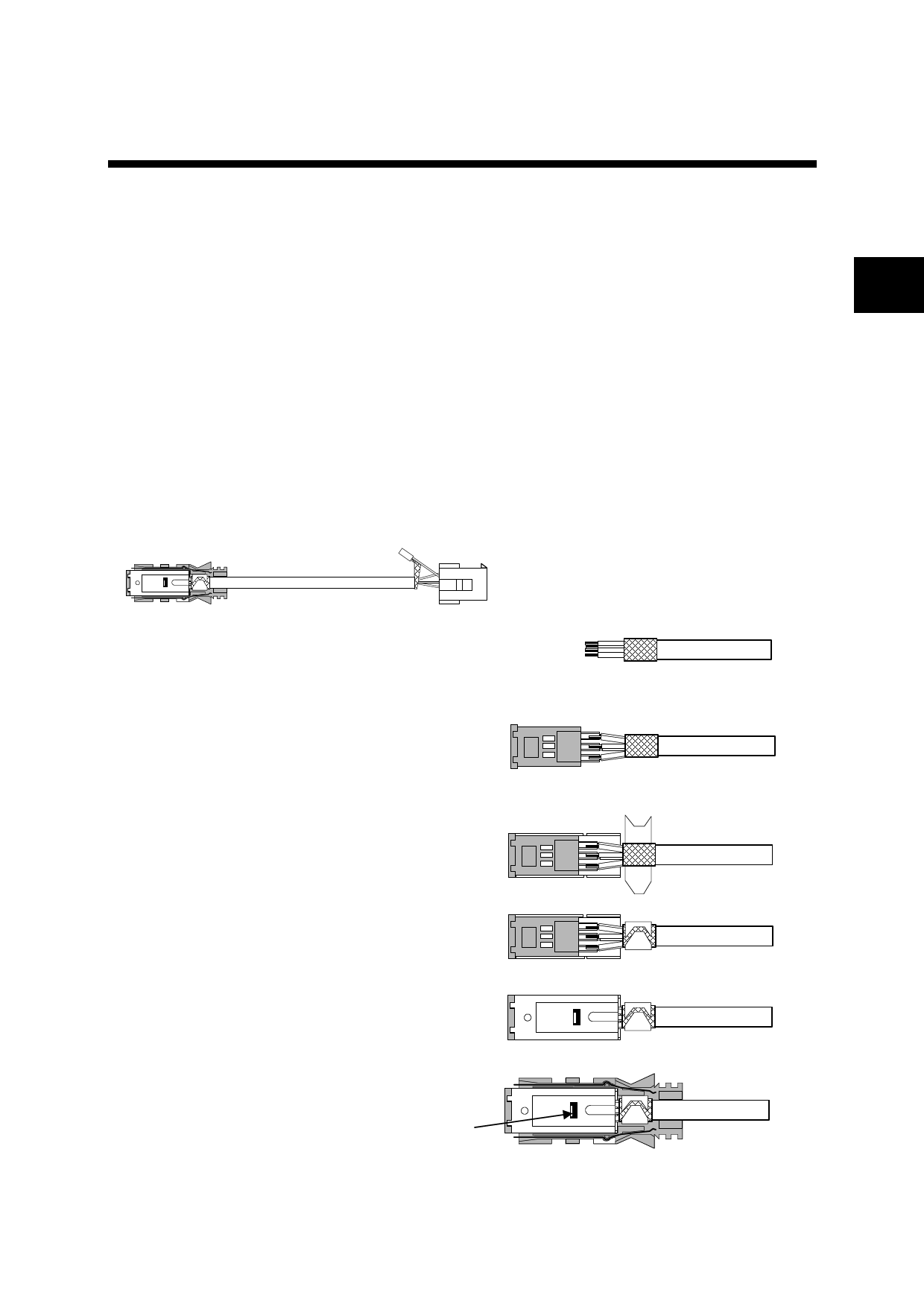
CHAPTER 2 WIRING
2.4.2 Encoder Cable
To fabricate the encoder cable by yourself, take care of the following.
Do not install a relaying terminal block between the servo amplifier and motor.
Use a shielded cable.
Connect the shielded cable with the designated connector pin, connector shell or cable clamp on
both sides.
The servo amplifier communicates with the encoder built in the servomotor through high speed
2
serial communications.
The shield treatment is important for the assurance of reliability of serial communications.
The maximum encoder wiring length is 50 m.
When twisting the cable, combine the following pair of signals.
P5 and M5, SIG+ and SIG-, BAT+ and BAT- (See the sample connection diagrams on pages 2-6
and 2-8.)
Please notice that wrong wiring may cause the encoder or battery trouble.
Perform shield treatment at the encoder according to the procedure specified below.
Despite motor capacity, wiring treatment at the servo amplifier is the same.
Encoder cable preparation method
Servo amplifier side
Motor side
Connect the end of the shielding wire on
the motor side to pin no.3.
Relay the shielding wire with a lead wire
of AWG#22 to 26 and then crimp the
wire to the connector pin.
[1] Peel off the end of the shield about 15 mm.
Fold back the shield.
Wind copper foil tape two or three turns around the shield.
[2] Solder the wiring to the connector.
The shrink tube wrapping each element cable
assures safety.
[3] Fix the connector to the shell cover.
[4] Bend the shield to fix.
[5] While aligning the catches on both sides, fit the
shell cover.
[6] Align the position of the catch to the mold cover to
fix.
Catch
Encoder 2-19