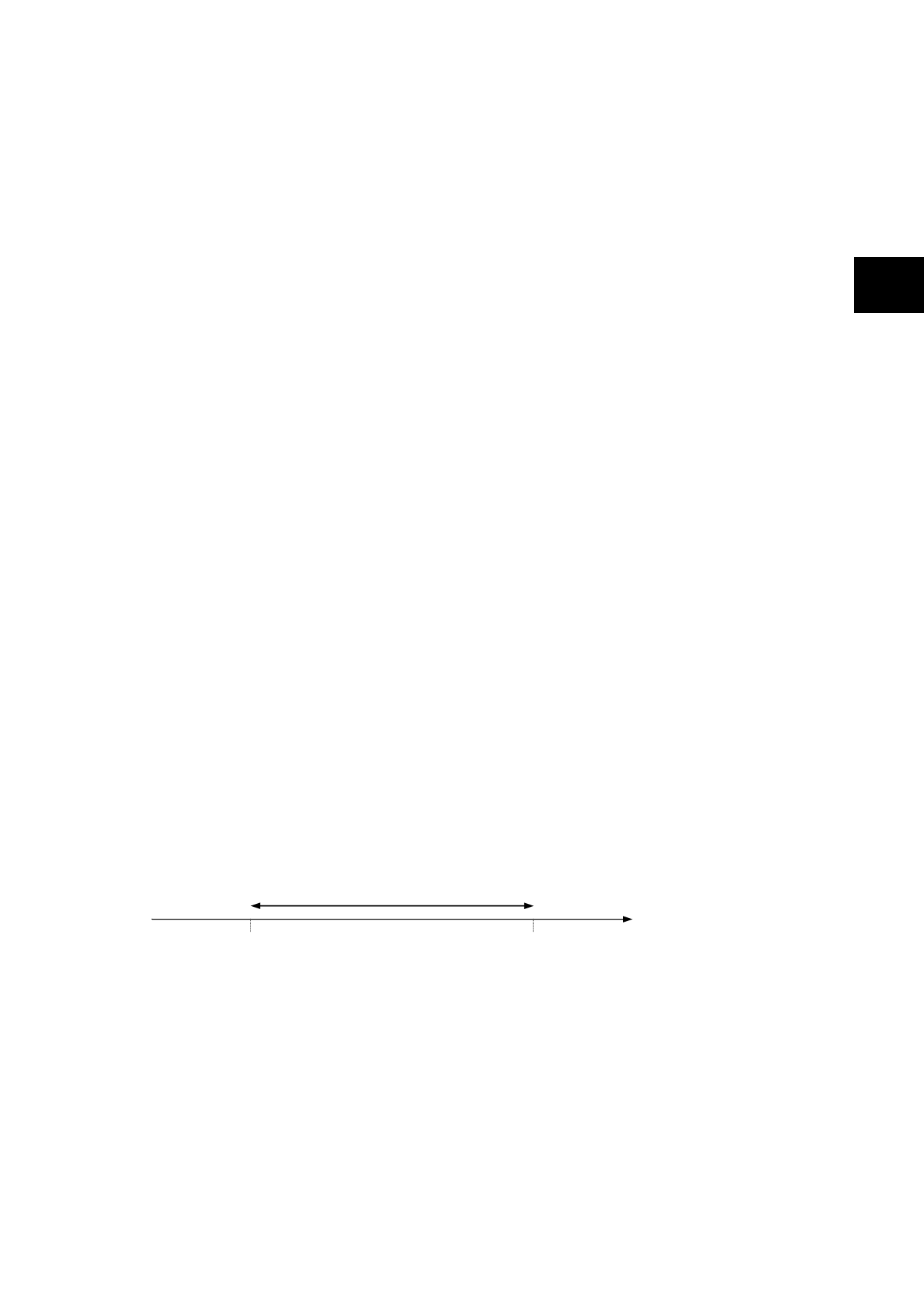
CHAPTER 2 WIRING
Parameter setting
To assign the +OT signal to a sequence input terminal, specify the corresponding value ("7") to
the input terminal function setting parameter. For the -OT signal, specify ("8").
Relevant description
(1) Direction of detection
The +OT signal is detected during a travel of the servomotor in the positive direction. The positive
2
direction indicates the direction of forward rotation if PA1_4 (rotation direction selection) is set at
"0" (positive direction). The servomotor is stopped, too, if a +OT signal is detected during rotation
in the negative direction, but it will not rotate in either direction.
(2) Output signal: +OT detection (38), -OT detection (39), OT detection (20)
The +OT detection and -OT detection signals indicate that the servo amplifier detects the limit of
travel in the mechanical system. A sequence output signal to the host controller can be notified
the fact of detecting the +OT or -OT signal.
The OT detection signal is turned on upon detection of either +OT (7) or -OT (8) or software OT
specified in PA2_26/27 (software OT detection position).
If the host controller is equipped with an OT input, connect to the host controller in general cases.
To specify this function, specify "38" (+OT detection), "39" (-OT detection) or "20" (OT detection)
in the output terminal function setting parameter.
(3) Software OT
Specify "1" (enable) to PA2_25 (software OT selection) to operate in the position range between
(PA2_26: + software OT detection position) and (PA2_27: - software OT detection position).
If this range is exceeded, forced stop will be caused with the OT detection sequence output.
Supply a pulse input in the direction opposite to the detected direction or perform manual feed
(forward / reverse command) to reset and travel in both directions.
The +OT (-OT) sequence input is for mechanical position detection, while software OT is for
position detection of the servo amplifier.
Traveling range
Negative software OT
detection position
(PA2_27)
Positive software OT
detection position
(PA2_26)
Feedback position
Description of I/O Signals 2-29