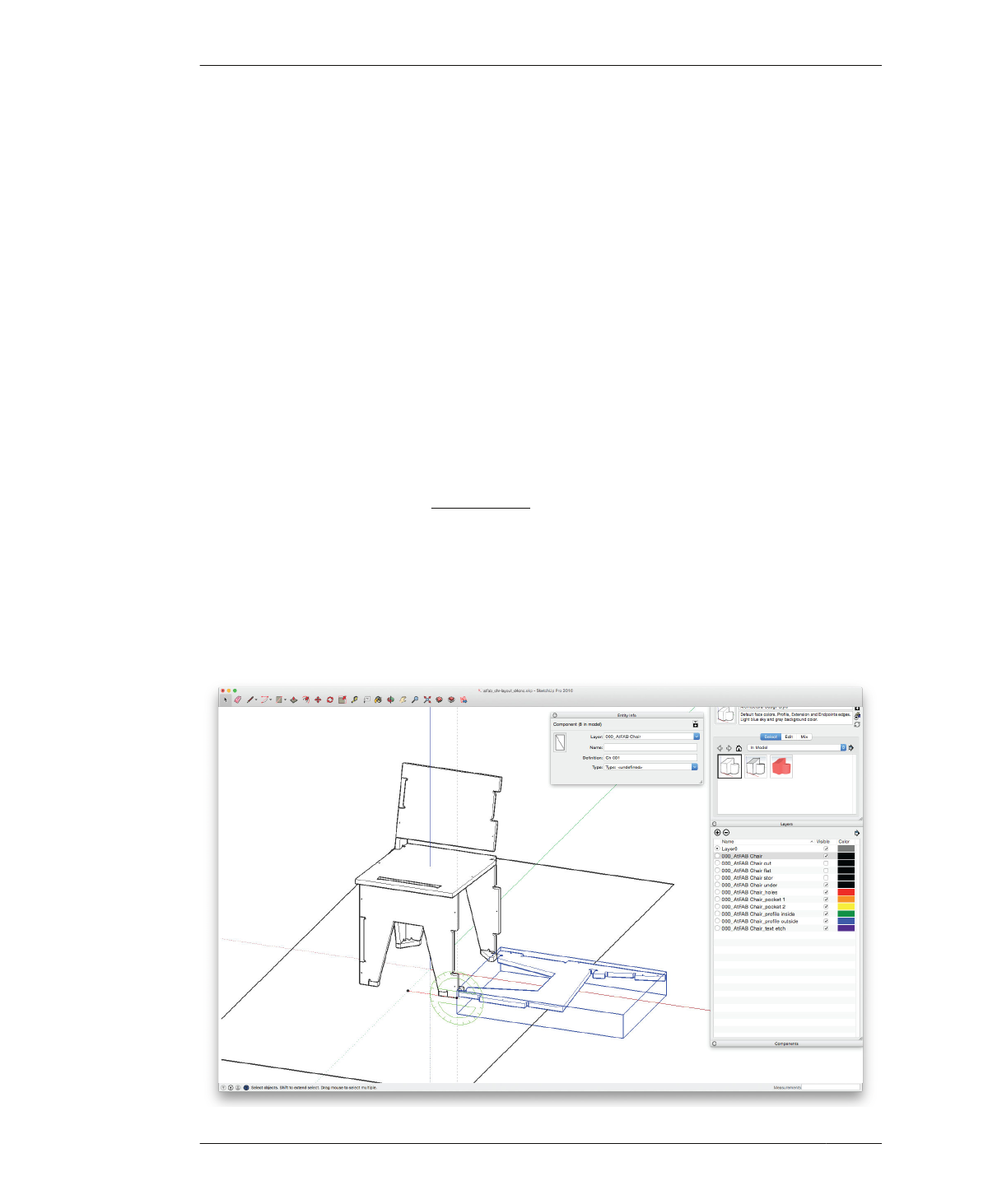
FLATTENING AND LAYOUT
FIGURE 3-4
Rotating the first chair
part onto the X/Y Axis
enough stock material left over to keep the part
in place. As the CNC cuts parts, the stock
material loses structural integrity. Parts placed
too closely together can vibrate out of place
and become damaged.
MINIMIZE MATERIAL WASTE
Finally, minimize material waste by laying out
chair parts to use as little sheet material as
possible. Once part orientation and grain direc-
tion are accounted for, keep moving parts and
nesting them into each other until you find a
layout that minimizes waste. While this exercise
focuses on one chair, you should find that two
chairs will fit within the sheet material bound-
ary.
FLATTEN AND LAYOUT PARTS
4A: Copy the entire model and paste it onto the
flatten layer, 000_AtFAB Chair flat (Figure 3-4).
4B: Turn off the original model layer,
000_AtFAB Chair.
4C: Select a part. Using the rotate or move
tool, rotate or move the part so that it is parallel
with the X/Y plane.
4D: Align the bottom face of each part with the
X/Y plane and material stock outline.
4E: Proceed with these same steps on all other
parts.
4F: With the bottom face of all parts aligned
with the X/Y plane, arrange each flattened part
within the material stock boundary, as shown in
Figure 3-5.
4G: Nest parts into each other so that material
is used efficiently, while maintaining a 1″ mini-
mum distance from the edge and between
parts.
COMPONENTS
The ten chair parts you’ve been working with
are comprised of six SketchUp components, a
collection of vectors and surfaces combined
into a single element. The Foot and Side are
76
DESIGN FOR CNC