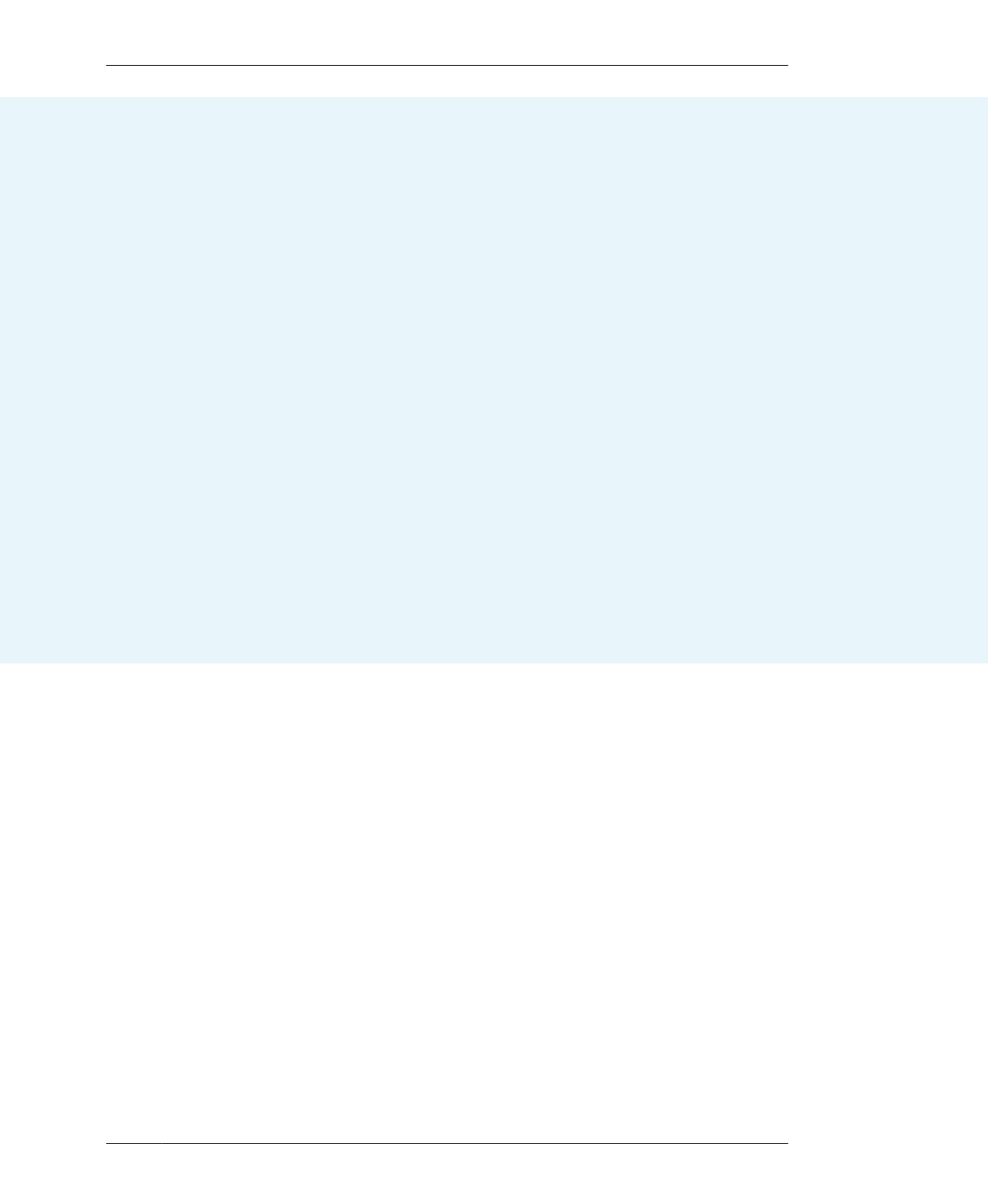
WHY DO CNC PROJECTS LOOK THE WAY THEY DO?
WHY I FOUNDED 100KGARAGES
I started as a ShopBot customer in the very early days,
when the only CNC tools were expensive industrial tools
costing $100k+. ShopBot founder Ted Hall saw their
potential and envisioned a way to make these amazing
industrial tools available to everyone, democratizing the
production of our everyday things. We imagined a future
where everyone would have a CNC machine in their
home and that we’d all make our own chairs, tables,
boats—whatever we needed—in new and interesting
ways. If we needed a new chair or table we would step
into our garage (or shed or spare bedroom) and fabricate
exactly what we wanted.
Later, we came to the realization that not everyone
needed to own a CNC machine. Most people simply
needed easy access to the output of these amazing
tools, so we started looking at ways to make that access
universal and 100kGarages was born.
100kGarages (http://100kGarages.com) is a free
resource that’s part matchmaking service and part “job
shop” facilitator, with a little bit of digital marketplace
tossed in to help people find interesting designs (like
AtFAB). The core function is to connect two types of peo-
ple: a “maker” who needs to have a thing made that ben-
efits from manufacturing by a digital tool of some kind,
and a “fabber” who has those tools. The maker may be a
mom who has a pencil drawing on a napkin of a sign for
her child’s door, a college student who wants an AtFAB
chair and has downloaded the digital files, or an entre-
preneur who needs 100 widgets made for a new product
and already has computer files of every detail.
The fabber could have a CNC machine or any number of
other tools—a laser cutter, 3D printer, or even a CNC
quilting machine. They could just be a cutting service,
but might also be a full-service fabrication shop that can
carry a project from design through finishing and assem-
bly. The fabber might own those tools, but they could
also be an entrepreneur working out of a makerspace,
fab lab, or other shared working space. The only require-
ment is that they are a legal business and that they
respect the intellectual property rights of the original
designer.
—Bill Young
tailed corners on an antique cabinet, or the
teak mortise and tenon joint in the arm of a
mid-century Danish chair.
The labor-intensive process required to manu-
facture affordable designs was gradually aban-
doned, when the mass-furniture industry
narrowed its optimization around lower costs,
manufacturing efficiencies, and lifestyle mar-
keting. In the process, style was separated from
construction, and any “look”—from Mission to
Shaker to Modern—could be appliquéd onto
lightweight particleboard parts. The inherently
fragile connections between these parts are
prone to failure. Structural loads and forces
easily weaken the points where hardware
meets particleboard. If you’ve ever moved from
one residence to another with particleboard
furniture, and had it rendered useless as the
hardware ripped out, you’ve experienced the
consequences of limited optimization.
Design for CNC has the potential to re-establish
the quality and integrity that has gone missing
in mass manufactured goods. The streamlined
production of intricate joinery, designed to
complement the structural capacity of modern
materials, can empower industry to once again
manufacture affordable, well-crafted, durable
furniture. Design for CNC also places this
industrial capability in the hands of the individ-
ual maker. The craftsmanship once achieved
only by the patience, labor, and skill of a master
woodworker is now in the hands of many.
01/A MODERN WAY OF MAKING
31