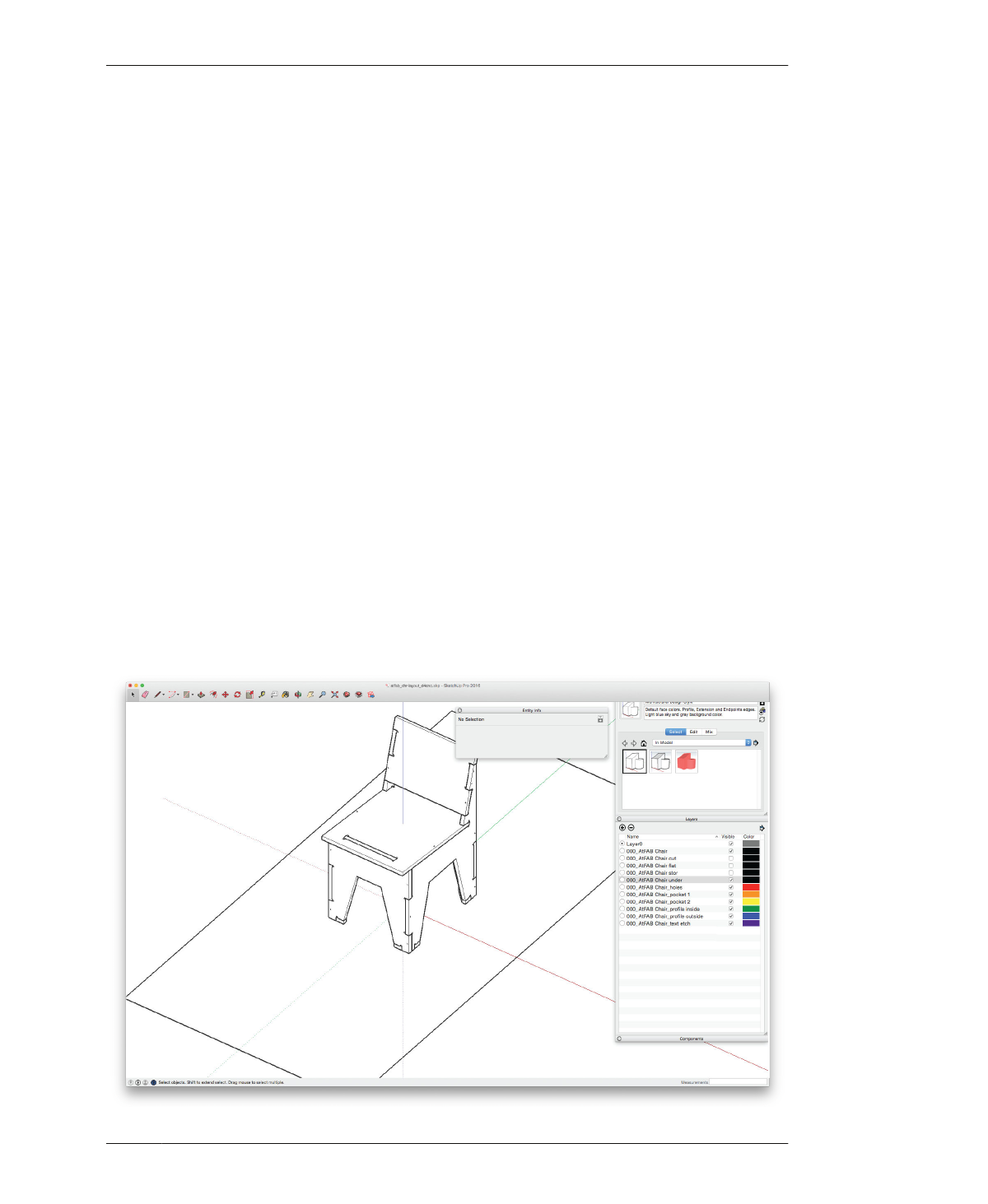
FLATTENING AND LAYOUT
of the seat and the exposed faces of the sides,
front, and back legs are facing upward, illustra-
ted in Figure 3-4 and Figure 3-5.
Face direction is key when working with sheet
materials, like plywoods, which often have dif-
ferent finish grades on each side (this will be
discussed more fully in “Selecting Materials”
on page 128). Face direction is also critical for
pocket cuts (see “Cut Pockets on the Correct
Side” on page 288), which must be milled from
the top surface of the sheet. This chair doesn’t
have pockets, but if you’re applying these flat-
tening techniques to another design, note any
design features as you lay out the parts.
Because every chair part is either symmetrical
or else a mirrored copy, its layout process is
more forgiving than a design that has asym-
metrical or multiple unique parts. If flattening
and laying out parts from a more complex
design, take special care that the correct sur-
face is facing upward. It frequently helps to
rotate and move parts into place on the sheet,
rather than mirror, to avoid cutting a backwards
part.
CONSIDER GRAIN DIRECTION
As you lay out each flattened part within the
cut sheet, give consideration to the direction of
wood grain across the part. There aren’t spe-
cific rules for handling wood grain, except to
look beyond just the part for opportunities
where the linear pattern can complement the
whole design. Grain direction may wrap around
a corner to emphasize volume, or it may run
lengthwise to emphasize slender proportions. It
may be parallel to the ground, while in in other
pieces it may be perpendicular.
LEAVE SPACE BETWEEN PARTS
Leave at least one inch between parts and the
material boundary. While it’s tempting to push
parts closely together, it’s important to remem-
ber that an end mill has a physical diameter
that creates a kerf when cutting. The tool needs
to fit between the parts, and there must be
FIGURE 3-3
Draw a 2D outline of
your material stock
03/3D MODEL TO 2D PARTS
75