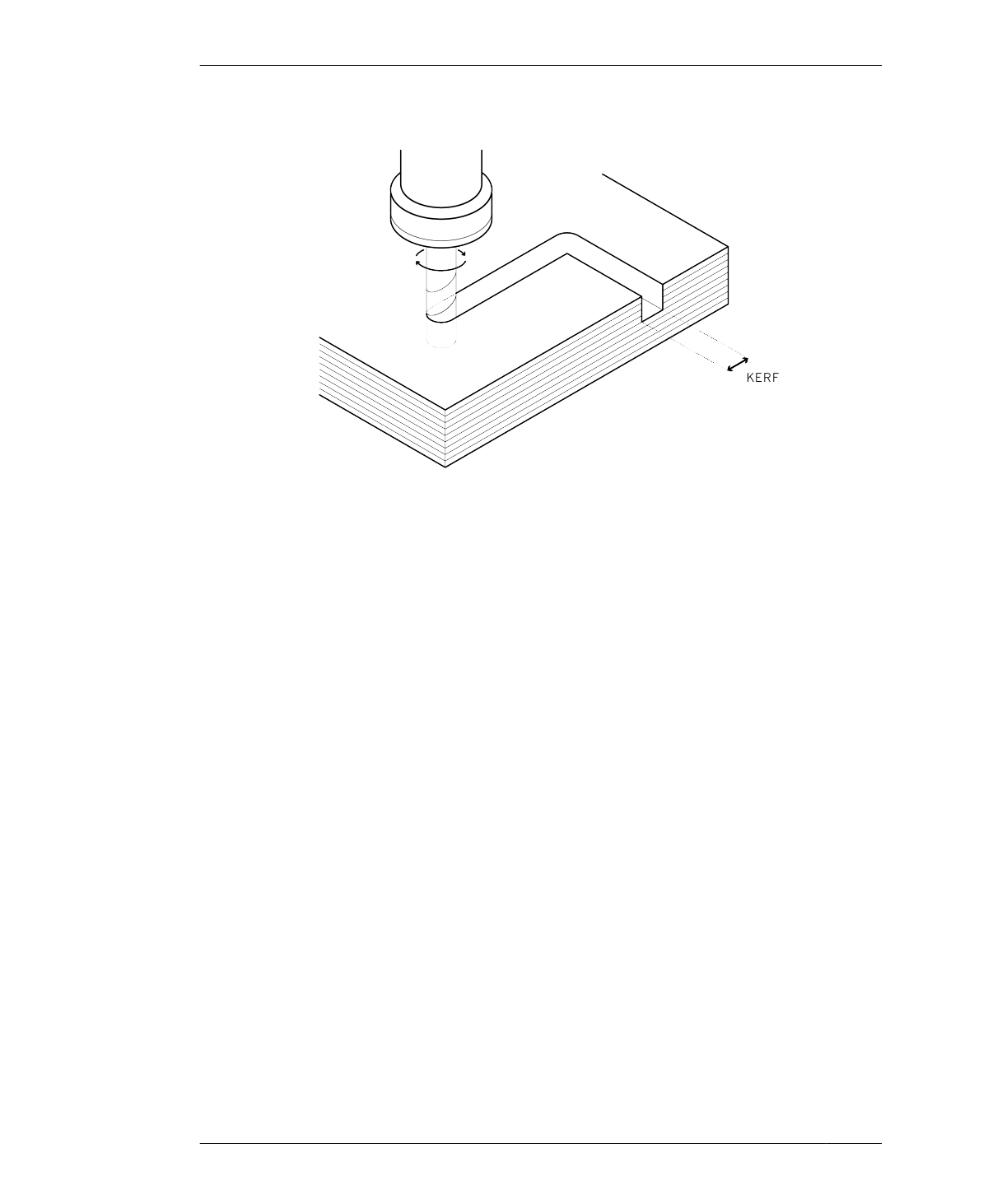
TOOLPATHS
FIGURE 2-10
An end mill traveling
along a profile toolpath
creates a kerf as it cuts
TOOLPATHS
Before taking a deeper dive into joinery, we’d
like to introduce a few basic CNC terms and
concepts.
CNC is an abbreviation for computer-
numerically controlled. A CNC machine creates
physical things from digital design files.
Depending on its particular capability, a CNC
machine deposits, fuses, cuts, or carves mate-
rials to produce physical things. Designers
develop parts or objects in a computer-aided
design (CAD) software program and then
export the design file into computer-aided man-
ufacturing (CAM) software. CAM converts the
design geometries into toolpaths, a combina-
tion of 3D coordinates and physical settings,
that drive the physical movements of the CNC
machine.
The movements of a 3D printer, robotic arm,
and CNC router are all computer numerically
controlled. However, the term “CNC” has
become synonymous with subtractive
machines. In the context of this book, CNC
refers to the computer-controlled routers and
milling machines that use rotational cutters.
End mills follow toolpaths, or a series of three-
dimensional coordinates and codes, telling
them exactly how and where to move and cut
to move and cut. That may sound complicated,
but it’s actually quite straightforward. Tool-
paths trace the lines of a design file.
Just like a saw, the computer-controlled end
mill removes material as it traces a toolpath,
forming a gap called a kerf, shown in
Figure 2-10. A kerf is the total width of the
material removed by an end mill as it cuts,
roughly equal to the diameter of the tool.
The most basic toolpath types are profile,
pocket, and drill. While all three cut to user-
specified depths, there are core differences.
PROFILE TOOLPATHS
A profile toolpath follows a line of an individual
part. It’s the digital equivalent of cutting a pat-
tern by hand. Profile toolpaths, or profiles, cut
around a closed shape to a specified depth.
While there is only one type of profile cut, there
44
DESIGN FOR CNC