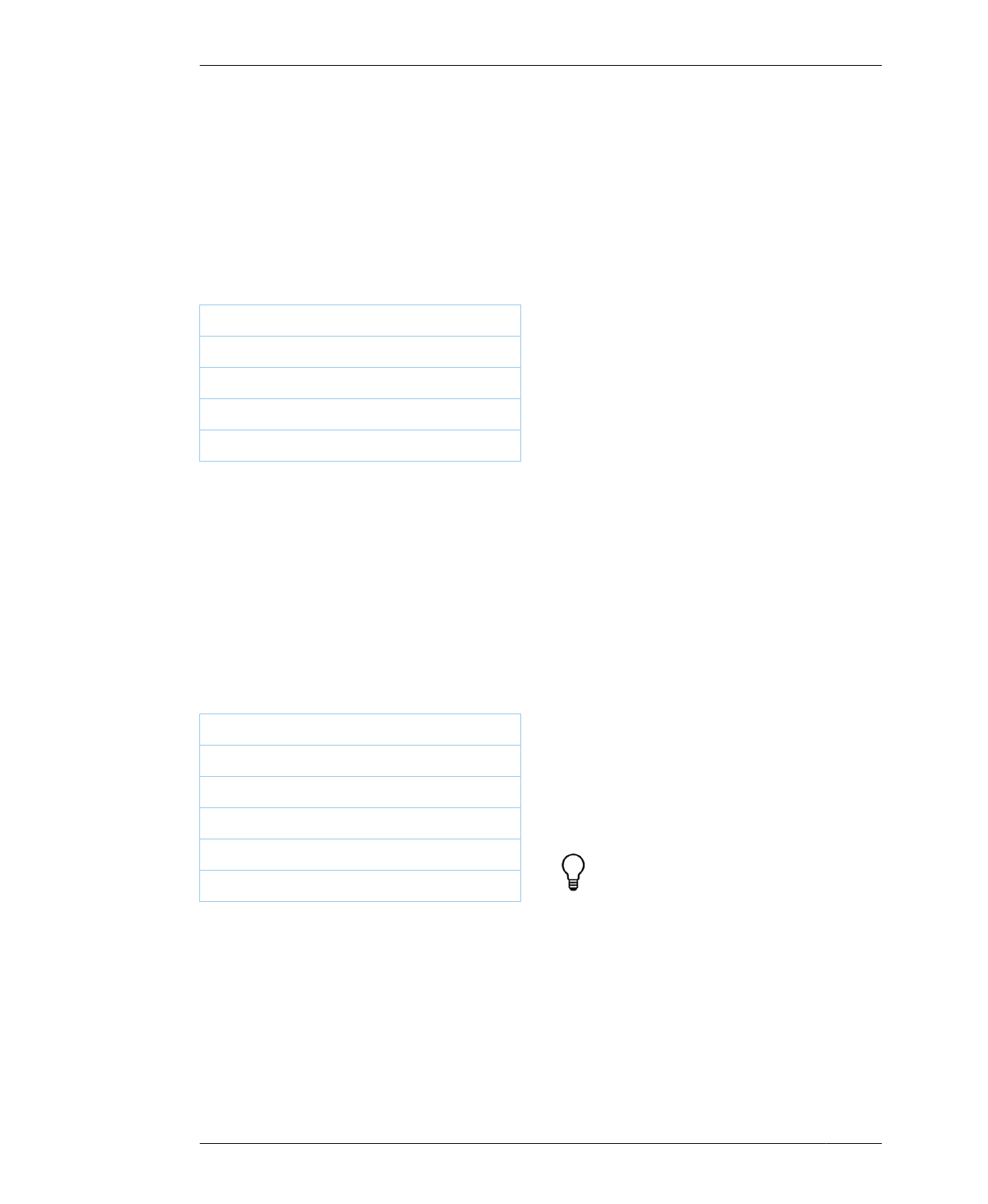
CREATE A PARTIAL PROTOTPYE
into the side, back, top, and bottom parts of
the Open Cabinet. Follow the steps for “Create
Pocket Toolpaths” on page 242, using a depth
of TCMAX/2.
The pocket toolpath settings are shown in
Table 14-1.
09: Position the outside-divider toolpath last in
the order. This place in the sequence allows
you to avoid the tool change, while switching
from the cabinet sheet material to the thinner
divider material.
CUT, ASSEMBLE, AND EVALUATE
TABLE 14-1. Pocket Settings
Tool Diameter
0.25 inch (¼″) end mill
Passes
2
Cut Depth
0.375”
Direction
Conventional
Toolpath Name
000 Outside Profiles
10: Save the toolpath operations for fabrication
and cut out the test piece parts from both
sheets. If you want to add a coating or finish to
your Open Storage Cabinet, test out the finish
on the test piece and evaluate fit.
11: Assemble the test piece, as illustrated in
Figure 14-9.
07: Second, assign an outside-divider toolpath
for the thinner sheet that simulates the shelves
and dividers. Set cut depth to match
TDMAX(e.g., ½″ (12)), keeping all other set-
tings the same as the outside toolpath.
The profile toolpath settings are shown in
Table 14-2.
TABLE 14-2. Outside Profile Settings for Dividers
Tool Diameter
Passes
0.25 inch (¼″) end mill
2
Cut Depth
0.51”
Machine Vectors Outside/Right
Direction
Conventional
Toolpath Name
000 Outside Profiles Dividers
08: When programing the cutting sequence,
cut fastener holes, pockets, and inside profiles
prior to cutting outside profiles. This order
ensures that small details stay aligned within
the parts as they are cut and minimizes the
number of required tool changes.
12: Evaluate the fit based on the description in
“Cut and Evaluate Fit” on page 201. To test the
depth of your pockets, the entire tab on the
shelf/divider part should be concealed by the
pockets.
If your test piece joinery doesn’t match the fit
described in “Cut and Evaluate Fit” on page
201, consult “Troubleshooting” on page 202 for
additional techniques and steps for achieving
an optimal fit. Continue cutting test pieces until
you are satisfied with the joinery.
13: Make a note of the scaling adjustment, and
save the final VCarve file (e.g., AtFAB_STG.crv)
that yielded the successful test piece.
If you’re working with a parametrically cus-
tomized file and run into any issues, you can
either follow the instructions in “Trouble-
shooting” on page 202 to scale the 2D profiles
in SketchUp, or return to the app to produce a
new file that better matches your material
thicknesses.
286
DESIGN FOR CNC