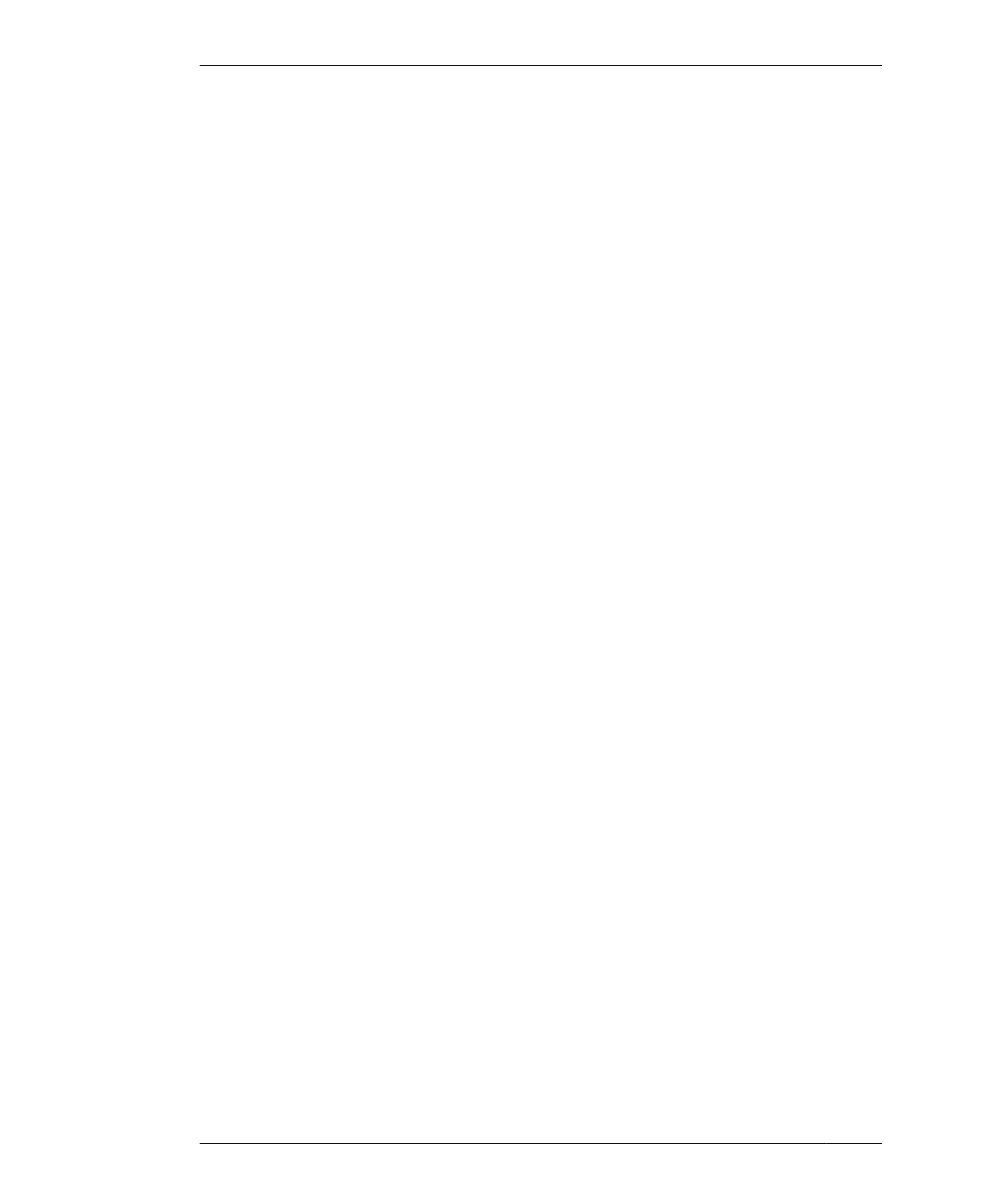
TROUBLESHOOTING
EVALUATE THE LIVELY STOOL
Just as before, piece all parts of the Lively Stool
together. Do the four legs interlock with a mod-
est amount of resistance? Does the opening in
the seat fit snugly over all four leg tabs? If all
five parts fit squarely and stay together on their
own, it means your CAM and machine settings
were correct, and your CAD file was scaled
properly to fit your material thickness (TMAX).
Whenever you achieve a perfect fit, record your
material measurements, CAD scaling, as well
as your CAM settings for future reference.
Fit is too loose
If the Lively Stool parts rattle around, and the
tabs of your Lazy Stool extend beyond the adja-
cent face, you scaled your CAD file by a per-
centage (S) that was too large to fit TMAX (see
“Scale Your CAD File” on page 133).
Fit is too tight
If it takes brute force to fit the Lively Stool parts
together, or they don’t fit together at all, you
scaled your CAD file by a percentage (S) that
was too small to fit TMAX. Turn to “Trouble-
shooting” on page 202 for tips on how to ana-
lyze further, so you can ultimately get a perfect
joinery fit.
TROUBLESHOOTING
Don’t get discouraged when your first round of
Rotational Stool or test piece parts don’t fit.
When starting out, easily assembled, perfectly
aligned joinery doesn’t always happen after the
first or second attempt. Getting to the perfect
fit simply requires additional scaling, or minor
adjustments to machine settings, and re-
cutting of your adjusted test pieces. This pro-
cess may feel quite tedious at first. However,
taking these extra steps at this stage will ulti-
mately give your furniture square joinery, solid-
ity, refinement, and a long, useful life. And, the
more you go through the process of trouble-
shooting, the more knowledge you’ll gain about
digital craft, and the better you will be able to
anticipate. When troubleshooting, start by
identifying the problem and then planning a
course correction.
MEASURE
When you don’t get the right fit immediately, it
first helps to understand the magnitude and
nature of the discrepancy. Take precise meas-
urements so that you can analyze the first out-
come, and course correct. Using calipers,
measure slots, tabs, and material thicknesses
of several parts. Measure the overhang or
underhang of a tab and adjacent face. Using a
pen and painter’s tape, mark up the stool parts
with your measurements and any additional
notes based on your analysis.
ANALYZE
Compare the material thickness measurement
of your parts with the original TMAX to ensure
that there wasn’t an error in your original mate-
rial measurements. Once you’ve determined
that the original TMAX matches your current
material measurement, look for consistencies
in your discrepancies. For instance, slots that
are larger than TMAX are usually accompanied
by tabs that extend beyond the face of an adja-
cent part. Both of these issues can arise as the
result of a CAD file that was scaled by too large
of a percentage (S).
Evaluate the edge quality of your parts. Parts
that easily release from the sheet and require
little sanding indicate that your tool and
machine settings were appropriate. If part
edges are rough, your machine settings may be
a factor. Chapter 6 offers more detail on the
variables that factor into ensuring quality CNC
machining.
202
DESIGN FOR CNC