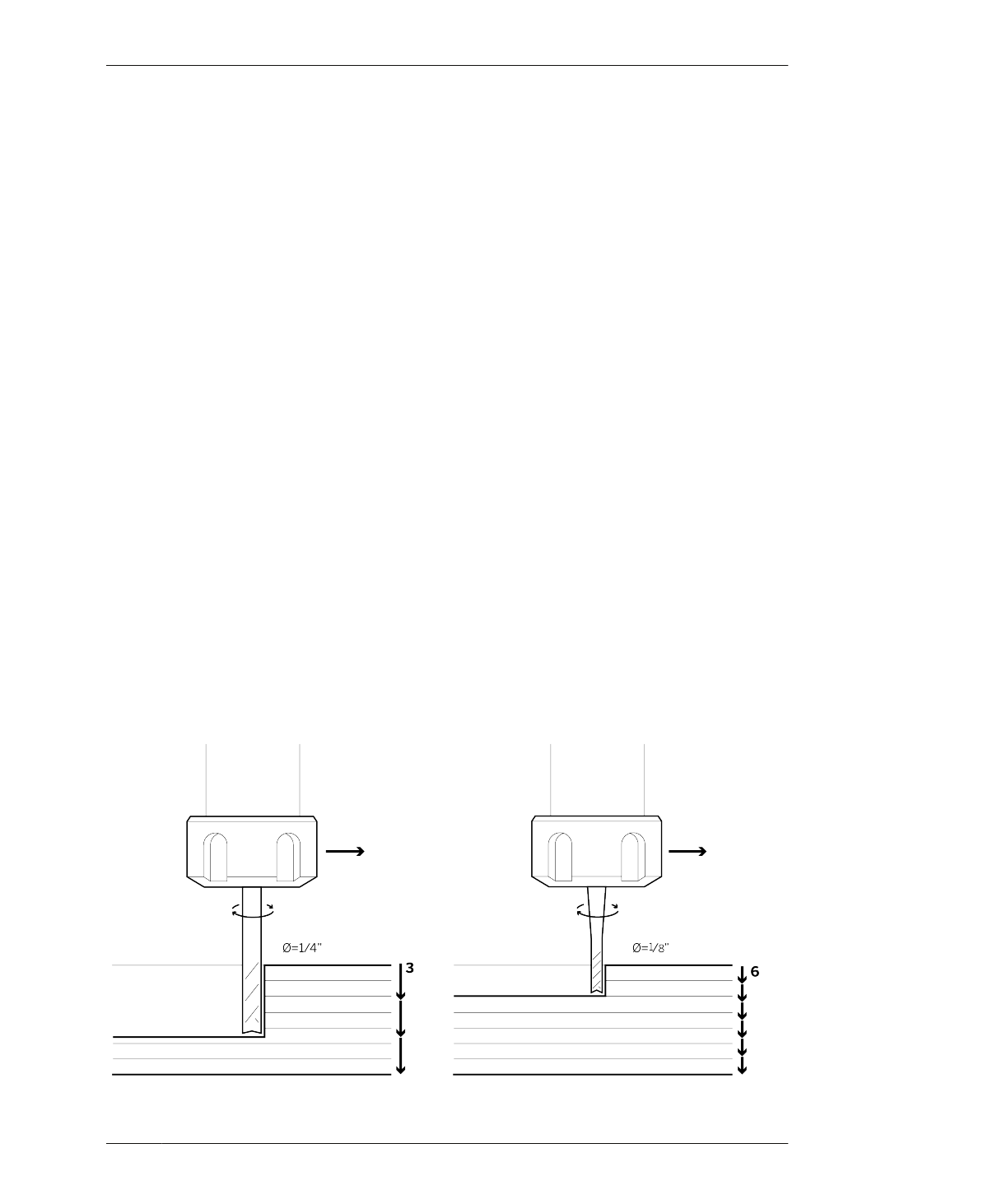
DEPTH OF CUT
hardwood than plywood. With plywood, you’d
need to determine what ply your cut depth will
reach, and which way the grain is rotated, a
tricky proposition.
STEPOVER
The amount of tool overlap between passes is
called the stepover value. The smaller the step-
over percentage, the finer the finish due to the
increased toolpath overlap. A stepover value of
50.0%, or one-half the diameter of the bit, is
usually enough to minimize tool marks and
leave a smooth bottom surface.
DEPTH OF CUT
Depth of cut, also called pass depth or depth
per pass, is how deep each individual machine-
cutting pass should be to reach the cut depth.
It often takes several passes to cut all the way
through material.
Depth of cut is determined by both material
thickness and end-mill diameter. When cutting
with small diameter tooling (1⁄8″ and smaller),
it’s best to make shallower passes than when
using ¼″ and larger diameter tools.
The general rule for determining depth of cut is
that one pass should equal the diameter of the
end-mill. So, as shown in Figure 6-12, a ¼″ end
mill takes three passes to cut through a ¾″
sheet of material or two passes for ½″ material.
Making more passes takes more time, but
makes a cleaner cut and puts less stress on
your tool. Increasing cut depth by too much
can lead to poor cutting quality, as well as end-
mill breakage. Experienced fabricators often
push cut depth to the limit to save time by
reducing the number of passes. However,
beginners and those with few tools might want
to err on the conservative side.
Both depth of cut and tool diameter have an
effect on chip load. When depth per pass
exceeds a tool’s diameter, the chip load
becomes greatly reduced. If your cut depth is
greater than two times the tool’s diameter, the
chip load is reduced by 25%. If you cut deeper
still, to three times the diameter, it’s reduced by
50%.
FIGURE 6-12
Pass depth for ¼″ tool
versus smaller 1⁄8″ tool
06/MACHINING FOR DESIGNERS
159