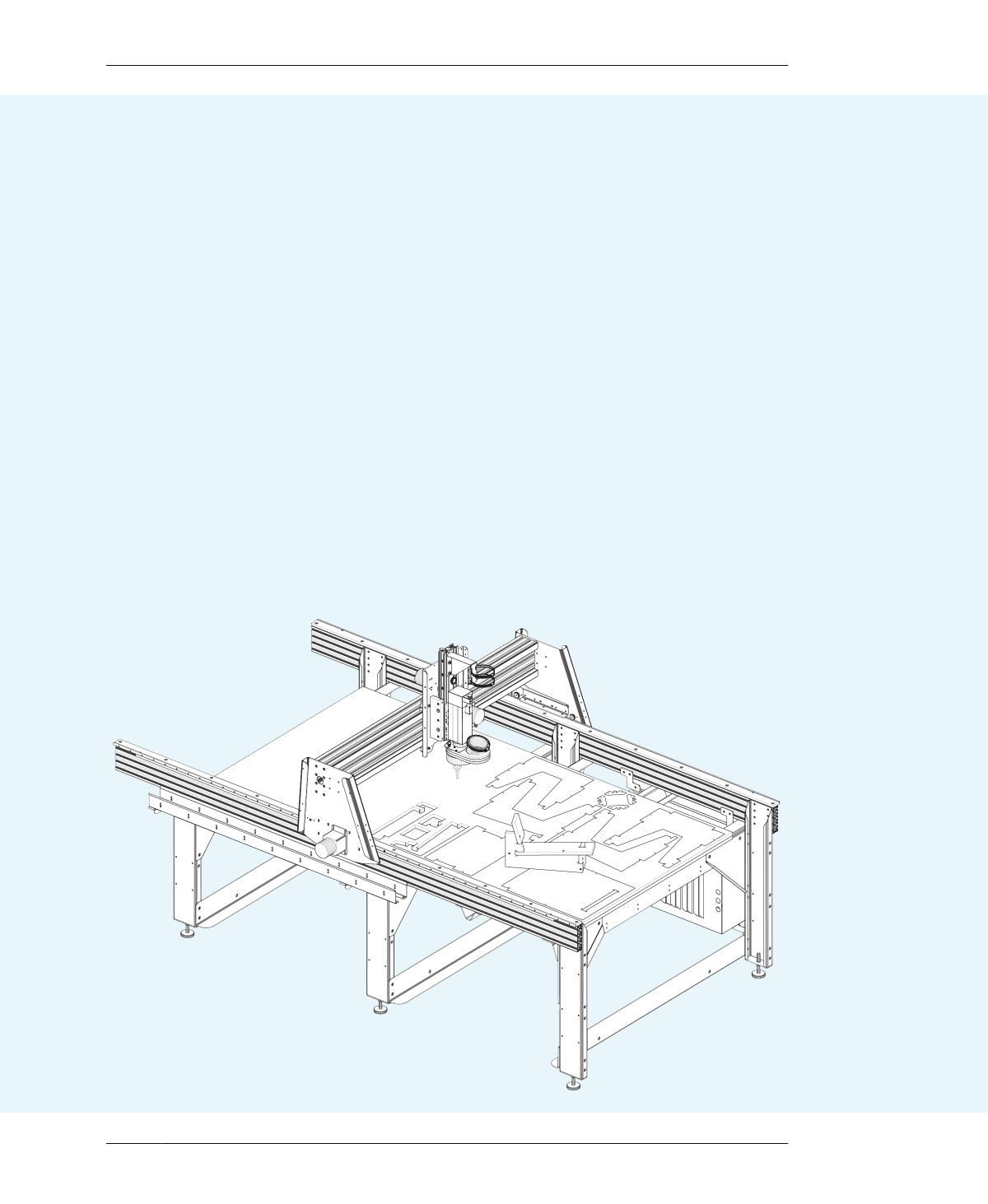
RAMP MOVES AND TABS
ROUTING STRATEGIES
When I need to access a full-size 4′ × 8′ router, I
head over to my local Fab Lab, where we use
screws for hold-downs on our ShopBot
PRSstandard. I hate cutting off tabs, so I always
use a downcut tool (Figure 6-7) when making
through-cuts, a trick I learned from Jonathan
Ward when we were at the Haystack Mountain
School of Crafts.
A downcut tool forces the chips down toward
the bed into the kerf, packing them around the
part to keep it from moving. The success of this
“no tab” downcut technique is dependent on a
plywood thickness-to-tool diameter ratio. It
works well for cutting large format parts from
¾″ or ½″ plywood using a ¼″ or 1⁄8″ diameter
tool. Larger tools create a bigger kerf, and chips
don’t always stay tightly packed, especially
when using dust extraction without a vacuum
system.
In his private shop on Virginia’s southern shore,
Bill Young uses a vacuum hold-down system on
his ShopBot PRSalpha. He uses a two flute
straight router bit (see “End-Mill Geometries”
on page 152) when working with plywood
because it yields a nice surface finish on both
the top and bottom of the parts, and lasts
longer than a downcut helix. Plus, this tool’s
cutting action doesn’t lift the part, helping to
maintain the vacuum and keeping the part
firmly anchored until the job is finished.
—Anna Kaziunas France
FIGURE 6-10
ShopBot PRSalpha 96″
× 48″ with assembled
test piece
06/MACHINING FOR DESIGNERS
157