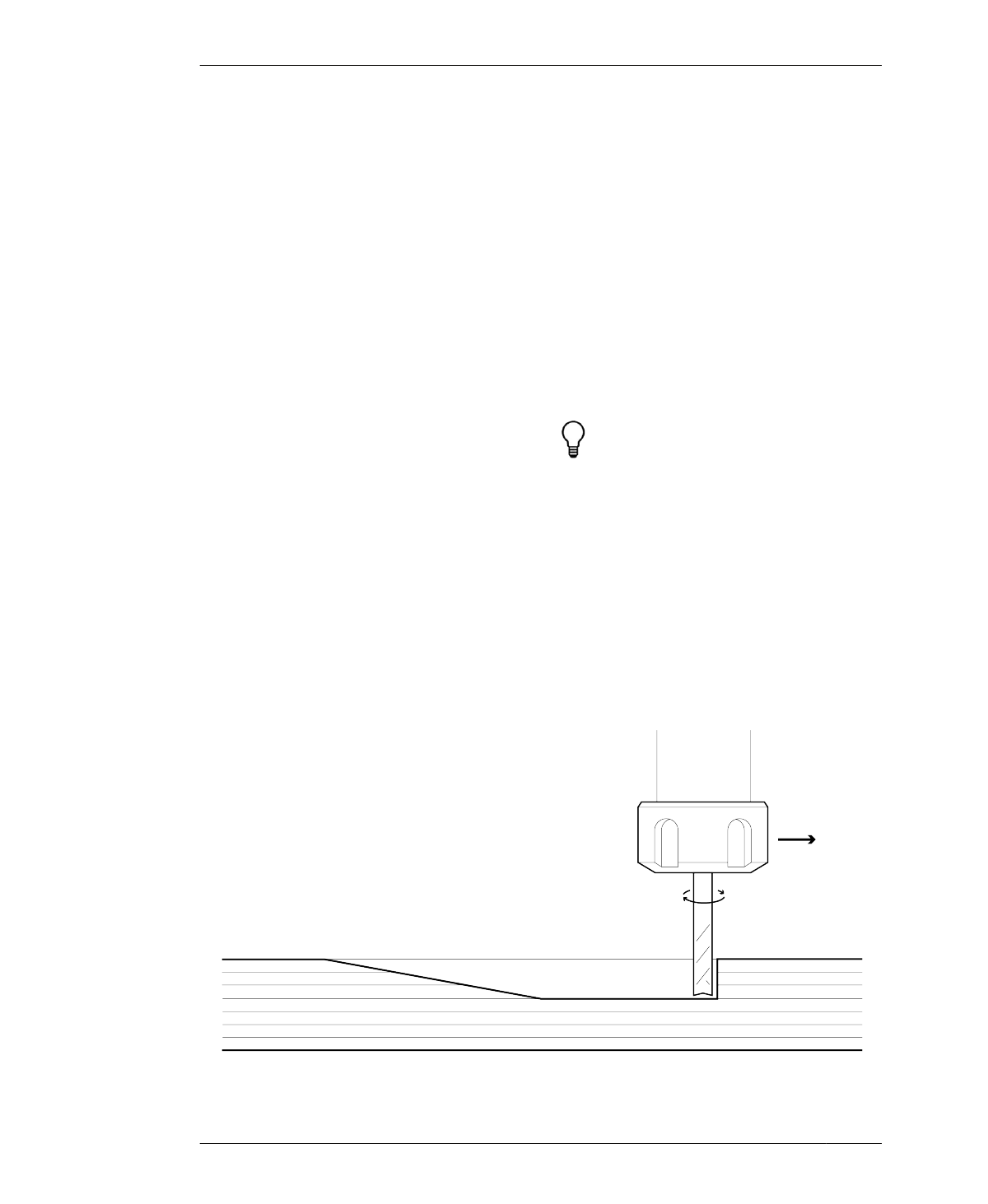
RAMP MOVES AND TABS
FIGURE 6-9
Smoothly ramping into
cut
axis load, plus it helps to reduce vibration and
keeps parts in place while machining. Because
you’re slowly ramping into the cut, keep your
plunge rate, or axial cut rate, the same as your
feed rate.
SMOOTH RAMPS
Smooth ramps work well for easing the tool into
large parts. Because center-cutting bits have
flutes on both the sides and bottom, and three-
axis CNCs can move in the x, y, and z axes at
the same time, it’s possible to gradually and
smoothly move the rotating tool into material
at an incline, as shown in Figure 6-9.
SPIRAL RAMPS
This ramp type slowly eases the tool into the
material over the full perimeter of a profile tool-
path. Spiral ramps are particularly useful for
small parts because machining forces can push
them around as they are being cut. If the part
becomes dislodged from the main workpiece, it
will get caught up by the moving tool, resulting
in ugly gouge marks in the part, which can also
fly off the machine bed. This is bad for safety,
your parts, and your end mills, which can break.
Spiral ramps also help to maintain vacuum hold
because they help to keep parts from lifting.
TABS
Tabs are small, rectangular sections of uncut
material, added to profile toolpaths in CAM
software, that keep a part joined to the waste
material when making through-cuts. Tab
length, thickness, and placement are usually
user configurable. Also called bridges, tabs are
helpful for keeping small parts in place or long,
thin parts from vibrating, especially if you don’t
have a vacuum hold-down system.
Pratical Tab and Ramp Advice
For most large parts, I use a four- to six-inch
smooth ramp into the cut, but with really
small parts (like feet) and holes I use a spiral
ramp. On small parts, I also use a single tab at
the start point of the cut and move the start
point so that it’s on a straight side that’s par-
allel to the grain. I rarely use tabs on large
parts unless they are long, thin, and want to
vibrate, and then a couple of tabs help.
—Bill Young
156
DESIGN FOR CNC