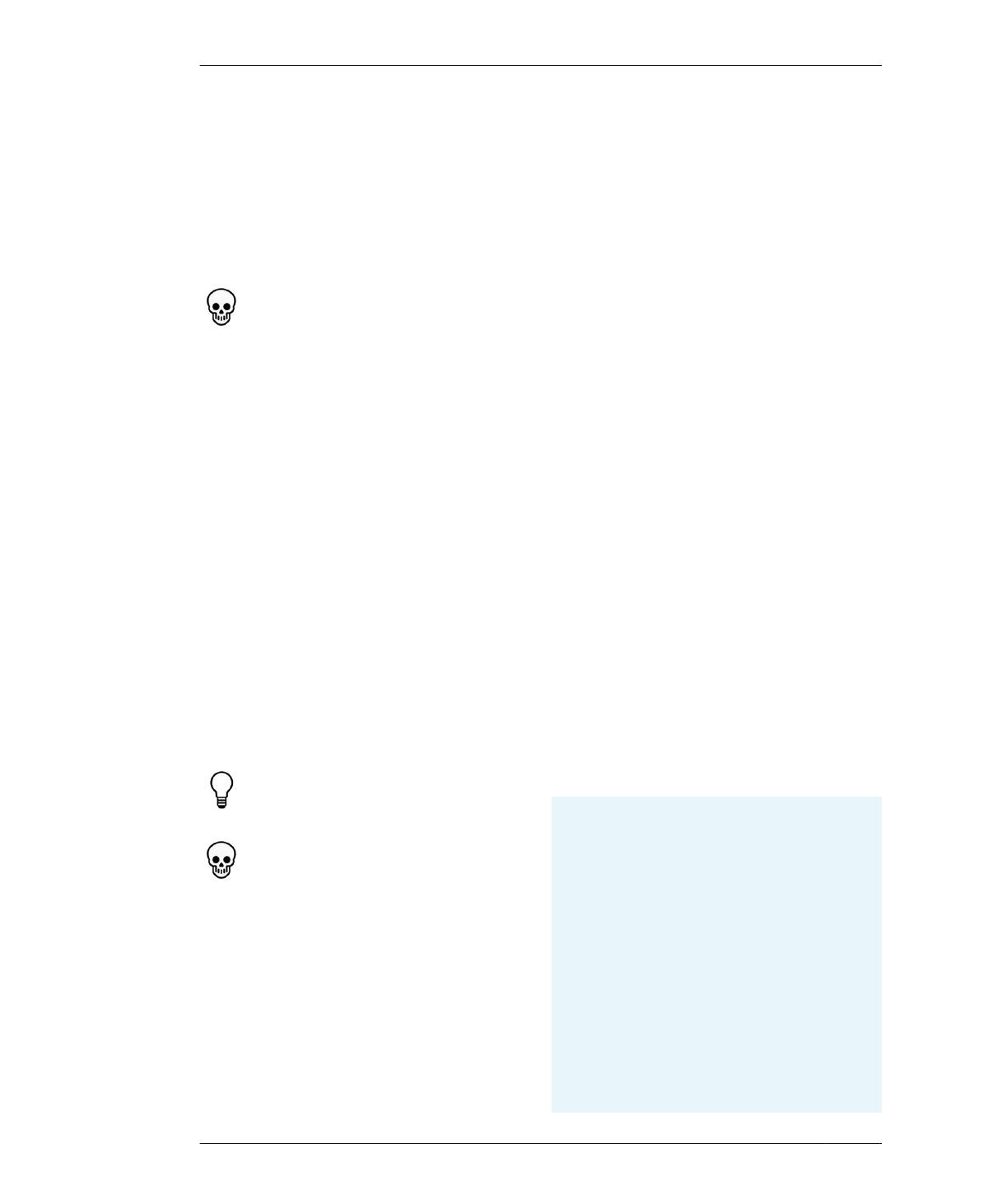
FEED DIRECTION
and 1⁄8″ downcut tools, the chips can become
compacted in the kerf, which helps to hold the
material against the CNC machine bed.
When through-cutting, the downward force cre-
ated by the chip ejection can cause tearout on
the bottom face, while the top face will have a
nice finish.
Don’t drill with downcut tools. It’s already
hard to clear chips when drilling, and pushing
the chips down into the hole further exacer-
bates this problem.
Compression Spiral
A compression tool is a combination of an
upcut and downcut spiral. It pulls material up
from the bottom of the cut and down from the
top of the cut, leaving a good-quality finish on
both the top and bottom faces. This seems
ideal, but compression tools are expensive, and
most are meant to cut in one pass at full depth.
Straight Flute
These radial two flute tools have a zero-degree
angle and create a superior finish in natural
wood and wood composites. The entire straight
flute makes contact with the material when
cutting. Chips are not pushed up or down, cre-
ating a good edge quality on most materials.
wood into a table saw, or metal into a station-
ary milling machine spindle. But when routing,
either with a hand router or a gantry-style CNC
router, it’s the opposite—you feed the spinning
tool into stationary material.
Feed direction determines which way the tool
moves around the part when cutting and how
the tool’s clockwise-rotating flutes create chips
when they make contact with the material. This
impacts the edge quality of your cut parts.
As illustrated in Figure 6-8, a conventional feed
direction cuts a closed part in a counter-
clockwise direction, while climb cutting moves
clockwise around a part’s perimeter.
CONVENTIONAL CUTTING
With conventional cutting, the primary cut is
made as the tool exits the material. The chip
starts out thin and then ends thick. This can
cause end-grain splintering in hardwoods, but it
works well for composite sheet goods, like ply-
wood.
This scenario is safer on a table or hand-held
router, and because hand-held routers paved
the way for CNC tools, this cut type is consid-
ered to be the “conventional way.”
Straight flutes are Bill Young’s tool of choice
for routing Baltic birch plywood.
Not all router bits can run at the highest avail-
able router/spindle RPM. The tools we recom-
mend are safe at high speeds, but you should
be aware that large diameter tooling, espe-
cially cheap, low-quality bits, may be unsafe to
run at max RPM. Refer to manfacturer docu-
mentation for safe speeds.
FEED DIRECTION
Material is often fed into machines—for exam-
ple, you feed fabric into a sewing machine,
ONSRUD TOOLING CATALOGS
Onsrud Cutter’s tooling catalogs are a great place to
learn about the wide variety of bits available. To
select a tool based on your project’s individual
needs:
• Download a Onsrud routing production tools cata-
log (http://www.onsrud.com/xDoc/brochures).
• Browse by material (plywood is composite wood).
• Find the appropriate geometry for your project,
taking cut type, part orientation, hold-down type,
and material into account.
154
DESIGN FOR CNC