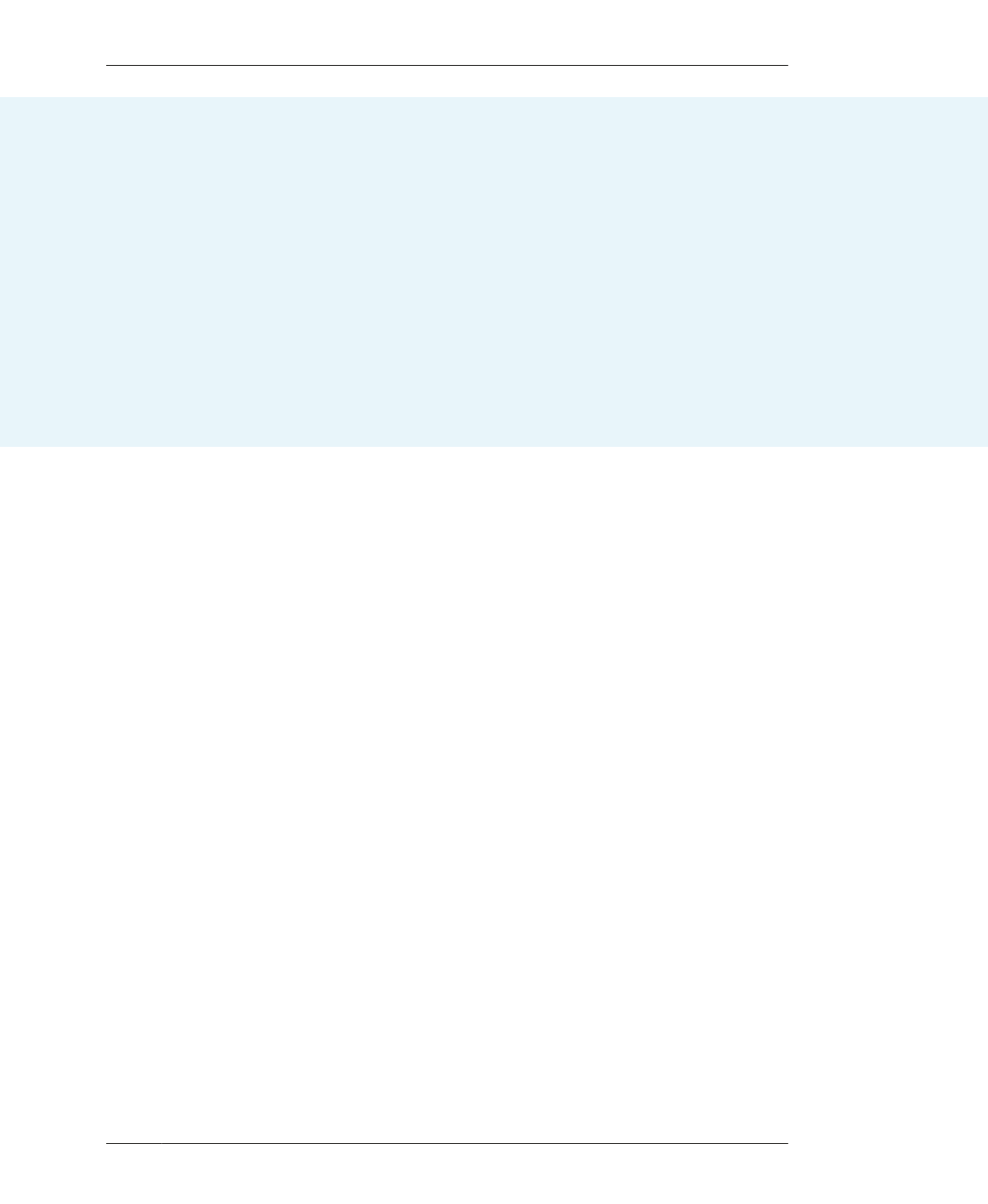
COLLETS
FINDING A CNC TO USE
You don’t need to own a CNC router to pursue any of
these projects. You simply need to find one near you.
Many community colleges and universities have shops
with digital tools. By signing up for a course, you’ll learn
how to use the machines and gain access to your institu-
tion’s facilities and equipment.
The recent proliferation of community makerspaces, Fab
Labs, TechShops, and other shared workshops, paired
with the increasing affordability of CNCs and increasing
educational focus on engineering and innovation, means
it’s easier than ever to get access to high-quality, reliable
machines.
In addition to CNC routers, most of these spaces offer
incredible access to an array of tools, software, classes
and workshops and are also typically equipped with
desktop 3D printers, laser cutters, and other tools that
make it possible to pursue a wide range of projects. We
always imagined that AtFAB could be a gateway DIY CNC
project at such a place, where you could start and finish a
project within the space of a weekend.
Cutting Edge Length
Abbreviated CEL, this refers to the part of the
tool that has flutes and teeth and is able to cut
material. Also called length of cut, LOC, or LC.
The cut length of an end mill determines the
maximum depth of cut (see “Depth of Cut” on
page 159).
Cutting Edge Diameter
Also called CED, this is the diameter of the cut-
ting edge length (CEL). It determines the mini-
mum feature size, or the smallest physical
detail that can be created when using a specific
tool.
Shank (SHK) and cutting edge diameter (CED)
are usually the same, but they can be different,
especially on smaller diameter tools. For exam-
ple, you can have a tool with a ¼″ SHK and a 1⁄8″
CED. See Figure 6-12.
Overall Tool Length
The overall tool length, or OAL is comprised of
both the cutting edge length (CEL) and the
shank (SHK). It determines how far the tool can
protrude from the spindle in the z-axis direc-
tion.
Deflection
It’s important to select the shortest overall tool
length with the largest possible diameter. The
farther a tool protrudes from the spindle, the
more it will deflect, or bend and flex, as cutting
forces are applied. While a small amount of
deflection always occurs when machining,
pushing a tool too hard (especially smaller
diameters) can create oddly angled cuts, dra-
matically shortened tool life, dulling, and
increased breakage.
COLLETS
A spring collet is a flexible type of chuck, or tool
clamping system intended to hold a cylindrical
object. The collet is part of the spindle assem-
bly. The tool is inserted into the collet and then
tightened with a collet nut that compresses it
tightly around the inserted tool.
Like end mills, collets also have dual diameters.
They come in standard sizes with an exterior
measurement that matches the CNC’s spindle
and an interior measurement that corresponds
to a tool’s shank.
06/MACHINING FOR DESIGNERS
151