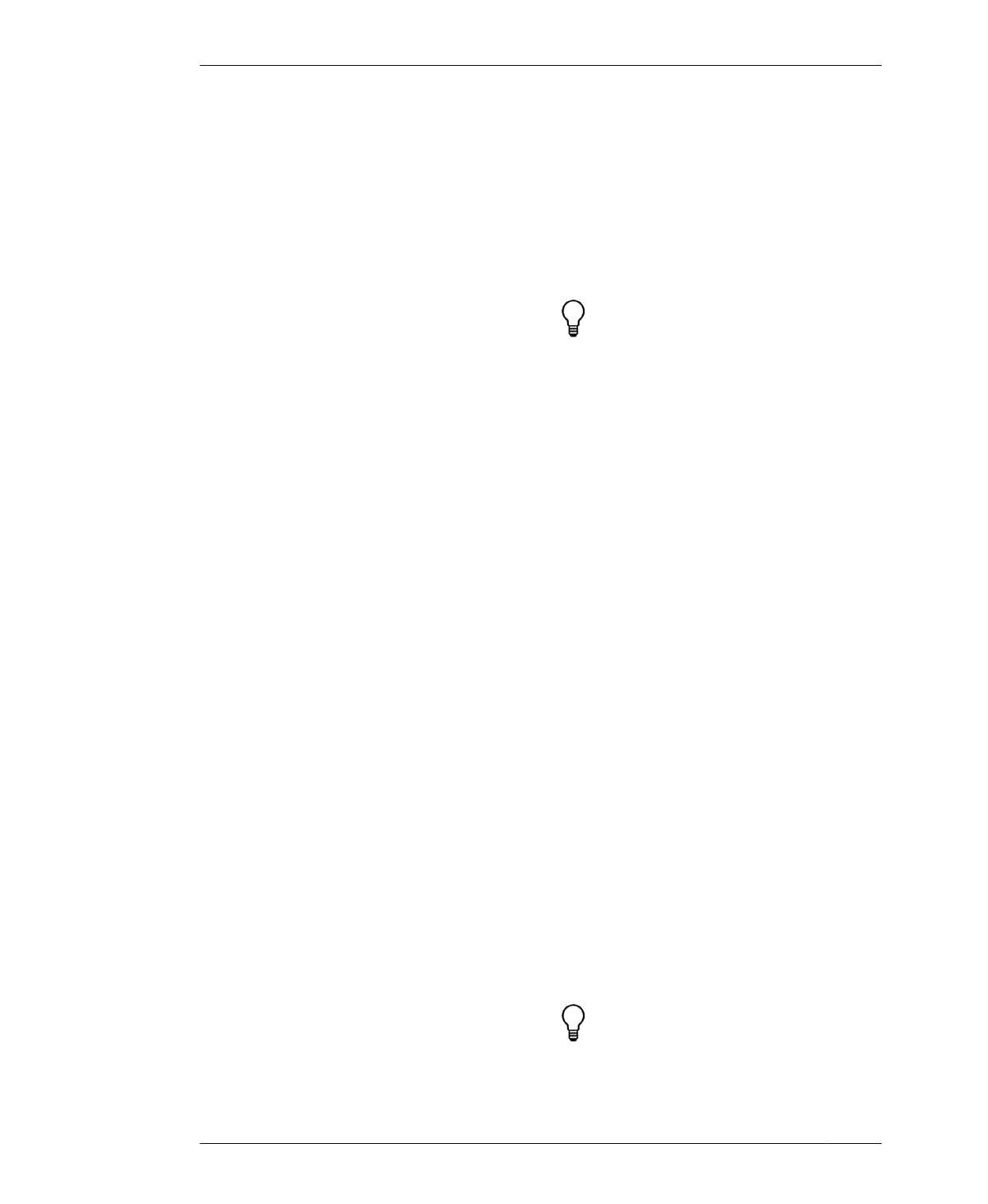
WORKHOLDING STRATEGIES
practice to always wear safety goggles and a
proper dust mask (if your shop doesn’t have a
dust filtration system). Plus, routers are loud
when cutting, so wear ear protection. Spinning
spindles can catch and pull in anything that
hangs loosely on the body, so always remove
jewelry, especially necklaces, and tie back long
hair and roll up your sleeves.
Clamps are very useful when working with
smaller size materials, or when you’d prefer not
to mar your workpiece with screw holes. How-
ever, clamps have one key disadvantage: they
protrude above the workpiece. This means that
you’ll need to account for them both in your
design and the toolpaths you create to avoid
hitting the clamp with the machine.
WORKHOLDING STRATEGIES
In order to cut the material, it needs to be
secured to the machine bed. There are two
basic ways to hold down material: mechanically
secure it to the bed, or use a vacuum system.
Your workholding strategy is important to con-
sider up front; hold-downs are physical objects
that you’ll need to factor into your design and
cut files. Mechanical hold-downs, for instance,
must be placed outside of the path of the spin-
dle and gantry, as collisions can cause tool and
machine damage. Decide on a strategy early in
your design process and keep it in mind when
preparing the cut sheet.
SCREWS AND CLAMPS
Mechanical hold-downs are off-the-shelf items
like screws and clamps. Screws are the easiest
and most common way to secure large sheets
to the sacrifice sheet. They don’t take up much
space, and they can be driven in flush with the
material being cut. As you cut sheets of 4′ × 8′
plywood for the projects in this book, it’s best
practice to add a screw at each of the corners
and then add additional screws approximately
every two feet around the perimeter of the
sheet. Carefully place the screws as close to
the edge of the material/machine as possible,
so you’ll be able to leave a 1″ margin around
your cut files and be confident that you won’t
hit any screws when machining.
Finding Safe Hold-Down Locations
Prior to cutting your actual design files, find
safe locations for screws and clamps in your
CAD/design files and then create a very shal-
low marking toolpath that creates “dimples”
to mark hold-down locations on the sheet.
After you run the marking toolpath, you’ll
clearly see the safe locations for adding
screws or clamps.
VACUUM SYSTEMS
A vacuum system uses suction to secure mate-
rial to the machine bed, enormously simplifying
the cutting process. It eliminates the need to
dedicate material to mechanical fasteners and
to plan toolpaths around them. Most signifi-
cantly, it speeds up the process of taking mate-
rial and parts on and off the machine.
There are two types of vacuum hold-down sys-
tems: conventional and universal. Conventional
systems are usually specific to a particular task
or process and utilize a small machine area,
where a universal system utilizes the entire
machine bed and is applicable to a broad range
of applications. When we mention a vacuum
hold-down in this book, we’re talking about a
universal system. Although typically more
expensive, they are well suited to jobs that
make through cuts in sheet goods.
A vacuum hold decreases the more through
cuts you make. You’ll want to limit the amount
of small parts and cut them first, while you
have more pressure.
148
DESIGN FOR CNC