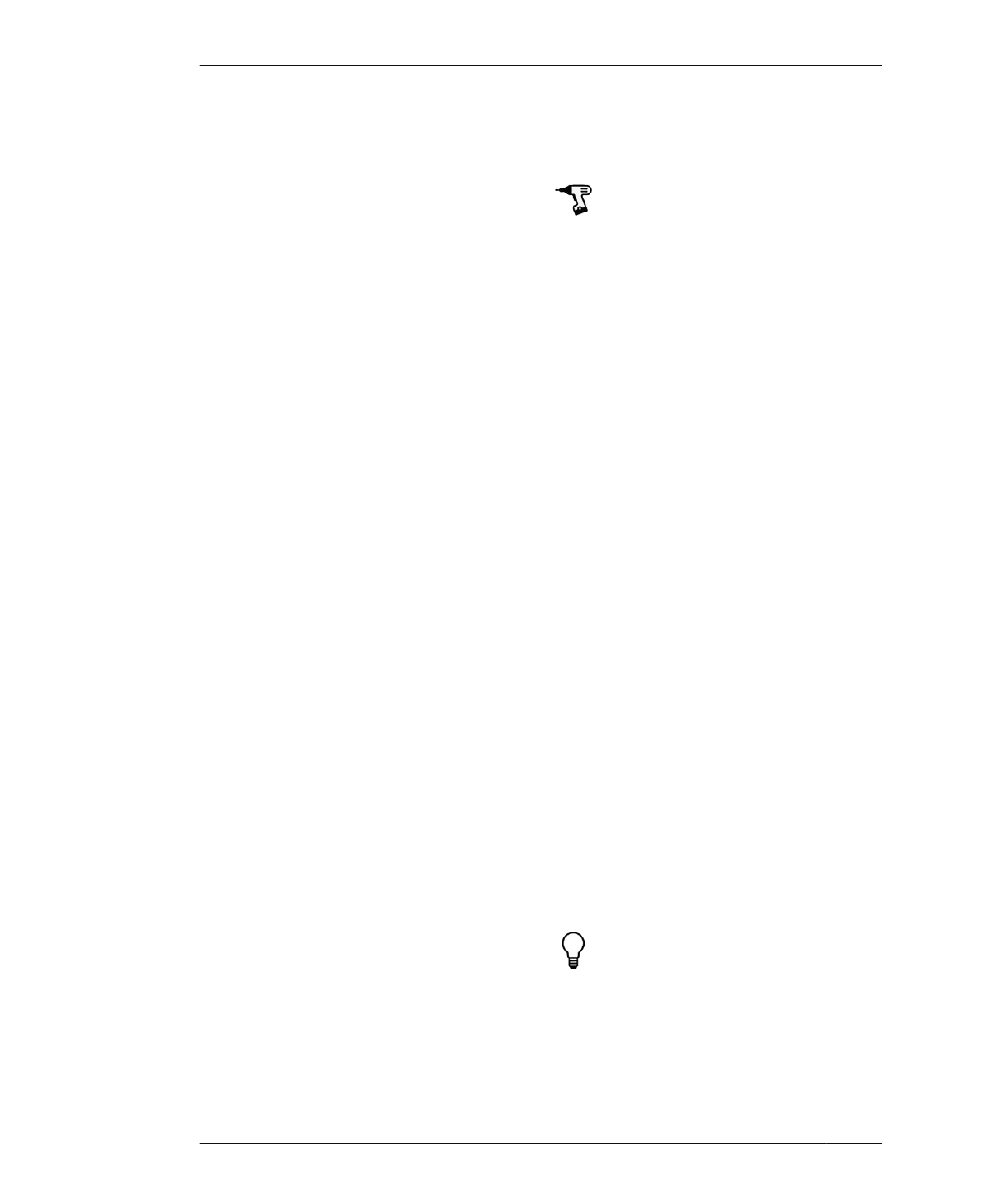
CNC ROUTER ANATOMY
WHERE TO BEGIN?
The interconnected nature of feeds, speeds,
and chip load are obvious from these equa-
tions. At first glance, this seems like a “chicken
and egg” problem. If all the variables are
dependent on one another, where do you
begin?
Start with what you know: namely, that you
want to cut plywood on a CNC router and that
you’ll need a router bit designed for that pur-
pose.
But before you can select a tool, you’ll need to
address the following questions:
• What type of CNC router are you using?
• What type of material are you cutting?
• What is the material thickness?
• How are the parts laid out?
• How is the material being held to the
machine?
CNC ROUTER ANATOMY
Large-format CNC routers are built for quickly
cutting softer materials by moving the cutting
tool through a full 4′ × 8′ sheet material, which
is fixed to a stationary bed. While the details of
such machines vary from manufacturer to
manufacturer, most share a common anatomy.
Rails
The rails are extruded aluminum tracks that
employ either a motorized rack and pinion sys-
tem or a v-rail/v-wheel linear bearing system to
create linear motion. The machine’s gantry, YZ
car, and spindle sit atop and slide along the
rails.
Gantry
The gantry is the y-axis of the machine; it sits
atop the long x-axis rails that run the length of
the machine bed. It holds the z-axis carriage
(and spindle) moving forward and backward
along the x-axis rails.
Machines that move the spindle around while
the material remains fixed are also called
gantry-style machines.
Desktop machines are likely to use rods and
leadscrews, or rods and belts, instead of rails.
They often secure the material to a moving y-
axis table while the spindle moves in the x-
axis.
YZ Car
It moves left and right on the y-axis across the
gantry, while carrying the z-axis and the
attached spindle.
Deck and Spoilboard
This is the flat, rigid surface where material is
placed for cutting, typically made of metal.
Deck size determines the maximum material
size that can be used on the machine. The deck
is covered with a protective, sacrificial layer,
also called a spoilboard or waste board. When
the spindle cuts through material, the tool
scrapes the top of the spoilboard, marring the
surface. The spoilboard is replaced when it
becomes worn out. The entire area (that is, the
deck/spoilboard combination) is also referred
to as the bed.
A bed doesn’t need to be flat like a pool table; it
just has to be parallel to the motion of the tool
(trammed). To ensure proper spoilboard/spin-
dle alignment, the sacrificial layer is placed on
the machine and surfaced by cutting away a
small portion of the entire top face with a large
bit. This preparation results in making the spoil-
board surface parallel to the motion of the tool.
Spoilboards need to be maintained and
should be resurfaced regularly. Deep grooves
in the waste board contribute to workpiece
vibration because they prevent the sheet from
lying completely flat on the bed. This vibration
is a key culprit in tool breakage.
146
DESIGN FOR CNC