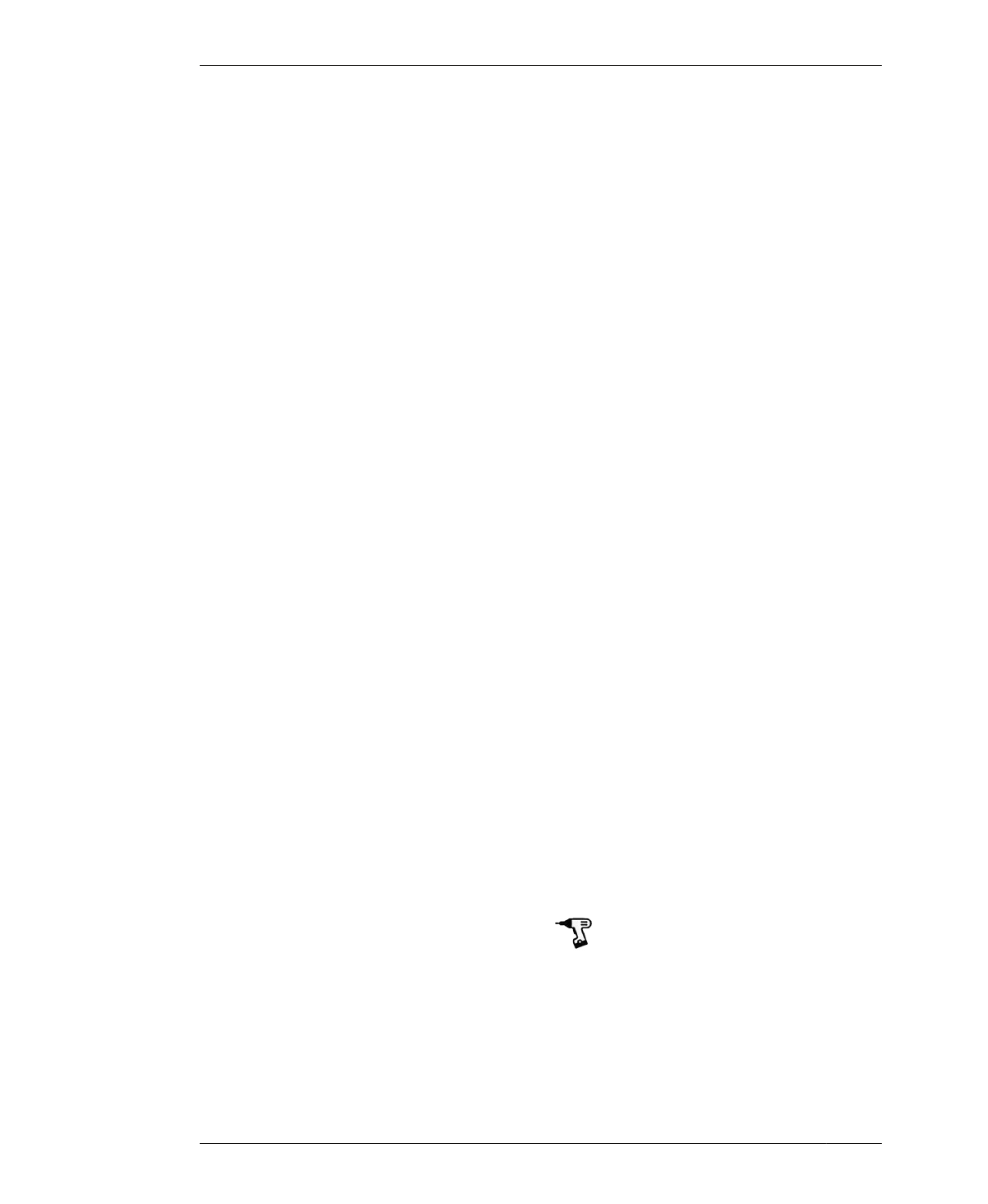
DESIGN DEVELOPMENT: JOINERY
DESIGN DEVELOPMENT: JOINERY
With parts defined, converted into compo-
nents, and organized into both 3D model and
the 2D cut sheet, you’re ready to move into the
smaller scale of detail. While the phase you just
completed is called schematic design, the next
phase, where you will be designing joinery, is
referred to as design development.
Thus far, you have modeled parts to “pass-
through” one another in an impossible way.
Early in the design process, it is sufficient to
sketch things in this way, so you can work
through the larger scale issues of your design.
Now that you’ve resolved the larger issues, you
can move onto the details, like composing
slots, tabs, and joinery at these points of over-
lap.
Chapter 2 explains how joints create an inter-
dependency between furniture parts, which
improves the structural stability of the bench
by distributing loads and forces evenly. To gain
the advantages of joinery, it’s critical to distrib-
ute joinery in the right places and to properly
position, orient, and size joints to maximize
contact between parts.
Take a look at your bench and identify the dis-
tinct conditions where parts converge and
where joinery should go. Start thinking about
what kind of joinery assemblies might be most
appropiate for each intersection (refer back to
“Eight Basic CNC Joint Conditions” on page
47).
This section takes you through modeling a ser-
ies of common joints for the bench. To keep
things simple, we’ll stick to mostly edge-to-
edge joints (also described as lazy fingers) for
joining the seat to the legs, the legs to the feet,
and the legs to one another. For the cross beam
that interlocks with the seat and sides, you’ll
model end-to-face and end-to-face-to-edge
joints. In the process of forming all of the bench
joinery, you’ll produce a corner assembly, tab
assembly, hanger assembly, and foot assembly.
Let’s get started by organizing the bench’s
many slots and tabs.
JOINERY ORGANIZATION
Finding some kind of order helps you properly
locate and distribute joints, and it facilitates
component repeatability. To give some order to
the bench joinery, we will orient details sym-
metrically, work with standard sizes, and keep
all joints consistently aligned to reference lines.
A clear, consistent ordering system like this will
coordinate our joinery placement with the pro-
portions of the overall bench, so joinery and
parts form a harmonious composition with the
object overall.
Before jumping into the steps of modeling join-
ery, it helps to first draw multiple reference
lines on Layer0. A datum and center line assist
you in precisely locating and aligning slots and
tabs. We will follow a process similar to the one
used to make guidelines for forming the U-
shaped bench legs.
In addition to working with reference lines, it
helps to find opportunities for consistency. It
will simplify things, for instance, to make all
tabs and slots one size that matches the 4″
(100 mm) dimension of the beam and legs. We
can always make adjustments later, but 4″ (100
mm) is a good starting point that will be easy to
manage while modeling the various details.
Imperial to Metric Units
These next steps will model 4″-long joinery
slots and tabs, which are ¾″ × ¾″ to match
the nominal material thickness. If you’re work-
ing in metric units, these slots and tabs are
100 mm × 19 mm × 19 mm.
106
DESIGN FOR CNC