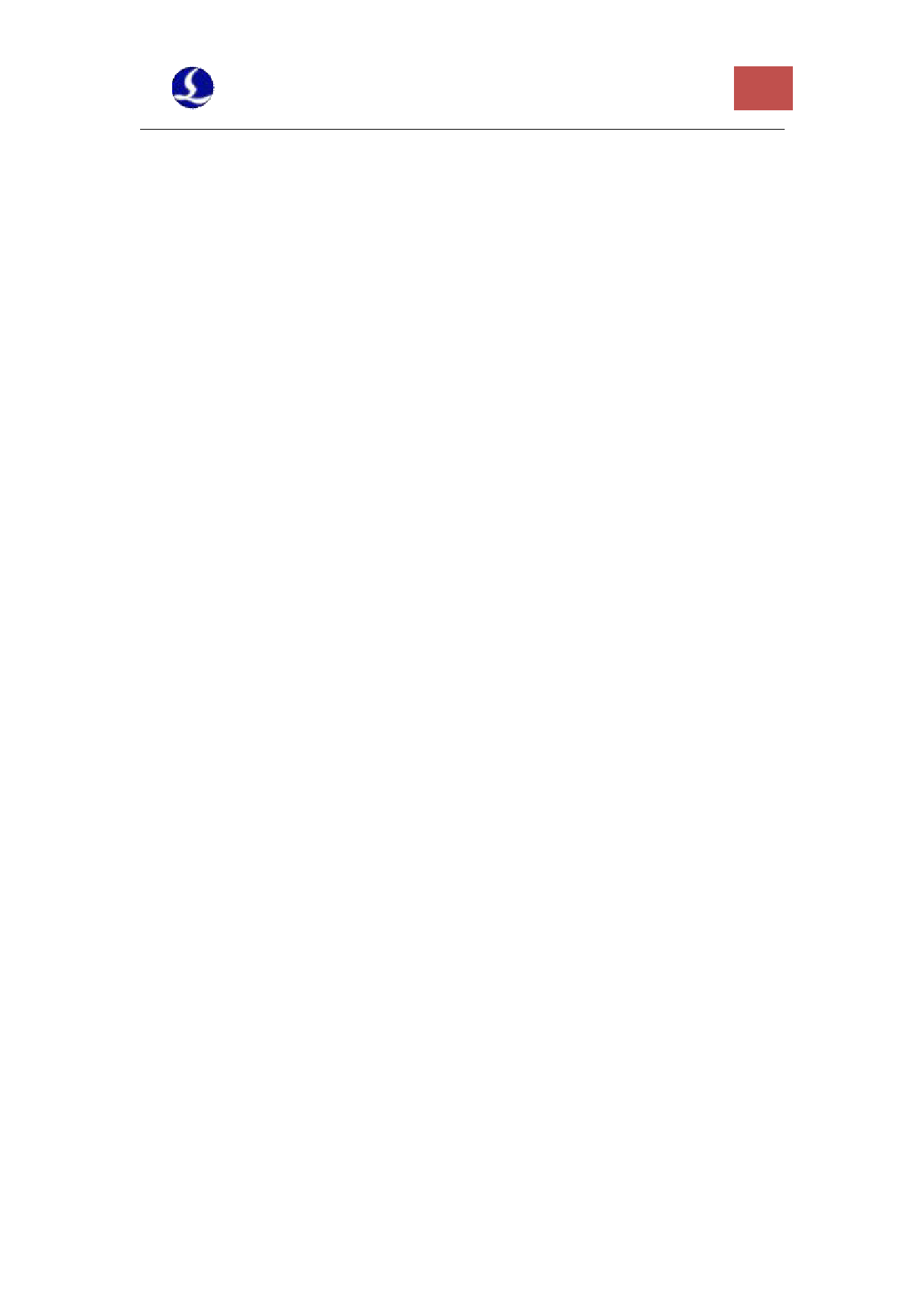
BCS100 独立式电容调高器
40
接线不良,零速钳位信号无效。
伺服刚性太弱。
编码器线被干扰,需要确认屏蔽层是否正确地接大地,最好再加磁环。
4.1.7 编码器无响应
当系统发模拟量出去,检测到编码器信号无任何变化时,会产生该报警。导
致该报警的原因包括:
接线不良,模拟量信号没有发到伺服中去,或者零速钳位信号一直生效,
或者编码器的反馈信号没有正确地接回到调高器中。
伺服选型不正确。不能选脉冲型的伺服,要选择带速度模式的伺服。
伺服参数设置不正确。没有切换到速度模式。
4.1.8 位置偏差过大
当系统检测到反馈回的位置和目标位置的差值过大时,会产生该报警。产生
该报警,一般标志着伺服系统无法正常地跟随调高器的位置环指令。产生该报警
的原因包括:
编码器方向反。系统的位置环没有形成负反馈。此时需要修改参数。
接线、干扰等导致编码器反馈不正常。
Z 轴机械卡住,系统瞬间扭矩增加,但是位置没有及时到位。
4.1.9 电容变 0
当系统无法正确地测量电容时,电容值会变成 0.以下原因可能导致电容变 0:
浮头接触到板面。
切割头进水。
切割头的本体电容太大,超出检测范围。
放大器损坏。
放大器/切割头的连线接触不良。
切割头内部,感应电容的正极(喷嘴)和负极(机壳)短路。
4.1.10 本体电容变小
当系统检测到本体电容变小超过一定范围时,会产生该报警。系统本体电容
变小的原因包括:
更换过配件,或者动过连接,或者本身模拟元器件特性的随机改变也可
能导致该报警。此时重新标定即可。
激光散射到喷嘴上,导致喷嘴温度急剧上升,产生温漂。
吹气导致正极(喷嘴)和负极(切割头外壳)之间的间隙改变。
放大器的连接线、喷嘴等接触不良。
标定距离设置偏小(3 维小于 10mm,2 维小于 15mm),也有可能会引起本
体电容变小的报警。
等离子云冲击电容放大器。在不锈钢板尤其是带膜不锈钢板的切割过程
中出现的概率较大。对于带膜不锈钢,请先去膜,再切割,不要直接带
膜切割(激光专用膜除外)。检查机床的接地情况,避免浮地,必须可靠
接地。跟随高度不要设置在 0.5mm 以下,适当增加跟随高度将有所改善;