- You are here:
- AM.CO.ZABuythisCNC Utilities Homepage
- RAYCUT-Fiber-Laser-Machine
- RAYCUT Fiber Laser Startup Parameters.pdf
- Page 12 of 26
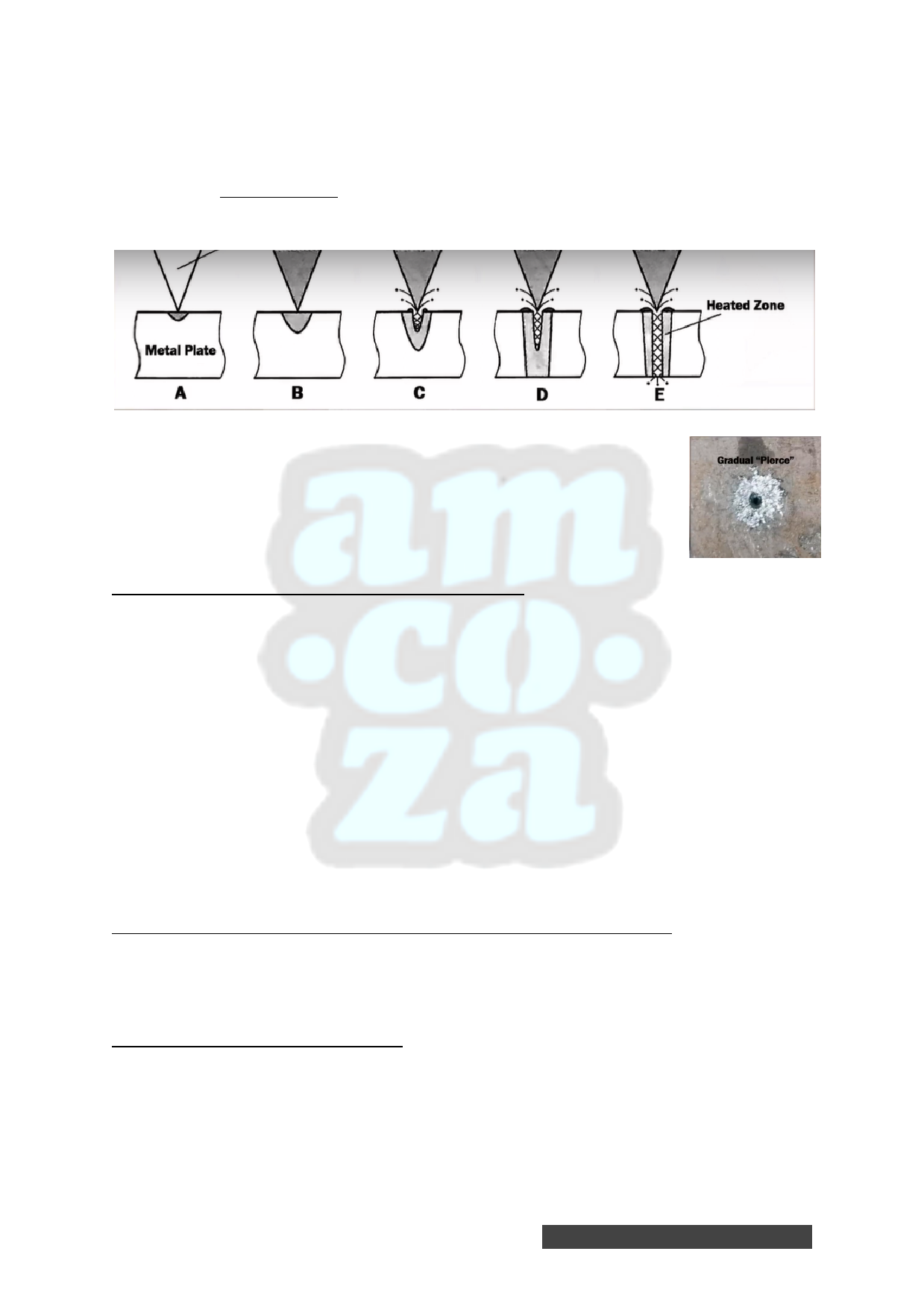
Because of the slag, this function is not required for machines with high accuracy
requirements.
We also have gradual-pierce which uses a laser pulse with high peak power and a low duty
cycle to melt and vaporise a small metal amount. This happens progressively until the sheet
is perforated. The diagram is shown below:
This process takes a relatively longer time as compared to a blasting
pierce but the results are however much cleaner. As shown in the picture
on the right:
In actual cutting however, a combination of the two types of pierce will be
used, especially in 3 stage piercing.
HOW TO CHOOSE A SUITABLE PIERCE TYPE:
● If the machine power is less than 3000W:
○ 6-12mm: 2-stage pierce with the first one being a blasting pierce and the
second one, a gradual pierce.
○ >12mm: 3 stage pierce with the first as blasting pierce and the second and
third as a gradual pierce (here we set the duty cycle <50)
● 6000W
○ 12-16mm: 2 stage pierce
○ >16mm: 3 stage pierce
NOTE: There's a definite figure on what the value for pierce setting is, so a good
practice is trial and error starting with no pierce to 3 stage.
: Two- Three stage pierce is mostly used for cutting carbon steel with oxygen gas
: Normally, one stage pierce is good enough for cutting stainless steel, Aluminum,
brass, etc.. using compressed air/ nitrogen gas.
Reasons for bland and uncut through holes on blast pierce could be:
1. High duty cycle
2. High Oxygen air pressure
3. High frequency
4. No stop blowing or the blowing time between multi-stage perforations is too short.
How to increase perforation quality:
1. Increase peak power
2. Lower the focus so that it’s at the metal surface.
3. Change the oxygen pressure of the pierce to match the cutting one or just switch
from oxygen to compressed air.
4. Increase the stop blowing time between multiple stage perforation.
5. To reduce the blowing pressure
BY NGONI CHIBVONGODZE