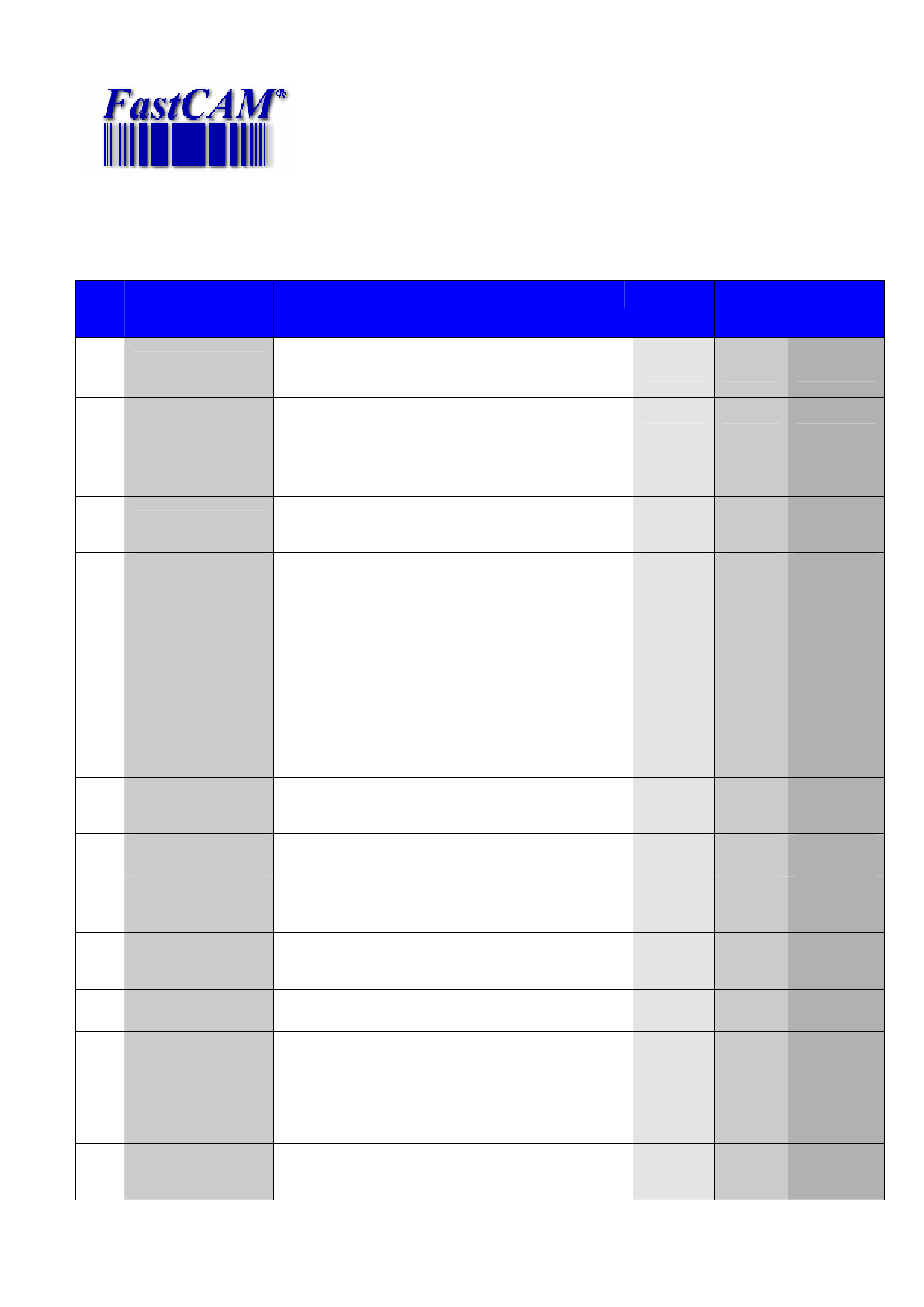
FastCAM® System
Feature Comparison Chart
Important Note: This table does not include every feature and function contained in the FastCAM
Systems. The intention is to highlight the main differences in the 3 versions.
Item
Features
Descriptions
FastCAM®
NC
FastCAM
® NC
Standard
FastCAM®
NC
Professional
1
Fully Integrated
Drawing System
Original Drawings Created without CAD Complexity.
2
DXF Import & Export
Data Exchange Format Most Commonly Used file format
for transferring files between CAD Systems.
3
IGES Import & Export
Internal Graphics Exchange System. Similar but more
powerful format than DXF. Usually found in very large
systems.
4
CAD Clean
Automatically removes unnecessary file data from
DXF files. Fixes common faults such as zero length
entities or overlays which cause machine stoppage.
5
CAD Compress
Reduces the Size of a CAD file, not the size of the drawing
but the computer file size. More important is that
any CAD systems will produce ARCS as dozens of single
tiny line movements. This is not suitable for cutting work,
and can cause serious, costly damage to the cutting machine.
FastCAM converts these back to true arc single line patterns.
6 Manual Part Extraction
from CAD files
A CAD file may contain entire assembly drawings which
may not be needed for a project. Any single part or piece
can be extracted for cutting from a CAD file without any
permanent modification to the original CAD drawing.
7
Bridging of Parts-
Joining of adjacent parts with small bridges for more
Standard
continuous cutting, minimizing piercing and implementing a
huge saving for plasma operations.
8
Multi Process Support
Multi process support for cutting, making, drilling, tapping,
etc. Support for all machine process as well as automatic
process detection from external CAD files by layer.
9
Multi language
FastCAM products can be supplied in all languages supported
Support
by the Window operating system.
10
CNC file on Screen
Simulates actual machine operation. Visually steps through
Verification
CNC code displaying process by color and line type
including piercing, drilling punching, mark, scribe, kerf, etc.
11 Reverse Engineering
CNC file conversion back to geometry using
a path from CNC through CAM and to DXF providing
complete flexibility for any format at input or output.
12
Printouts with
Customized Template
CAD like printing with layout which includes nest and /or
part data.
13
Blocks Array
Base Nesting
For rare and occasional nesting, requirements, blocks array
nesting may be performed.
This is accomplished by “blocking” a part, originally drawn or
imported and setting up “blocks copy” thereby creating an
array of almost any size and composition desire.
This would seldom if ever be employed by anyone but a
FastCAM NC user.
14
Interactive Nesting
A semi-automatic method of nesting parts on materials.
Single profile parts can be automatically nested onto a
given size plate.