Page 14 of 22
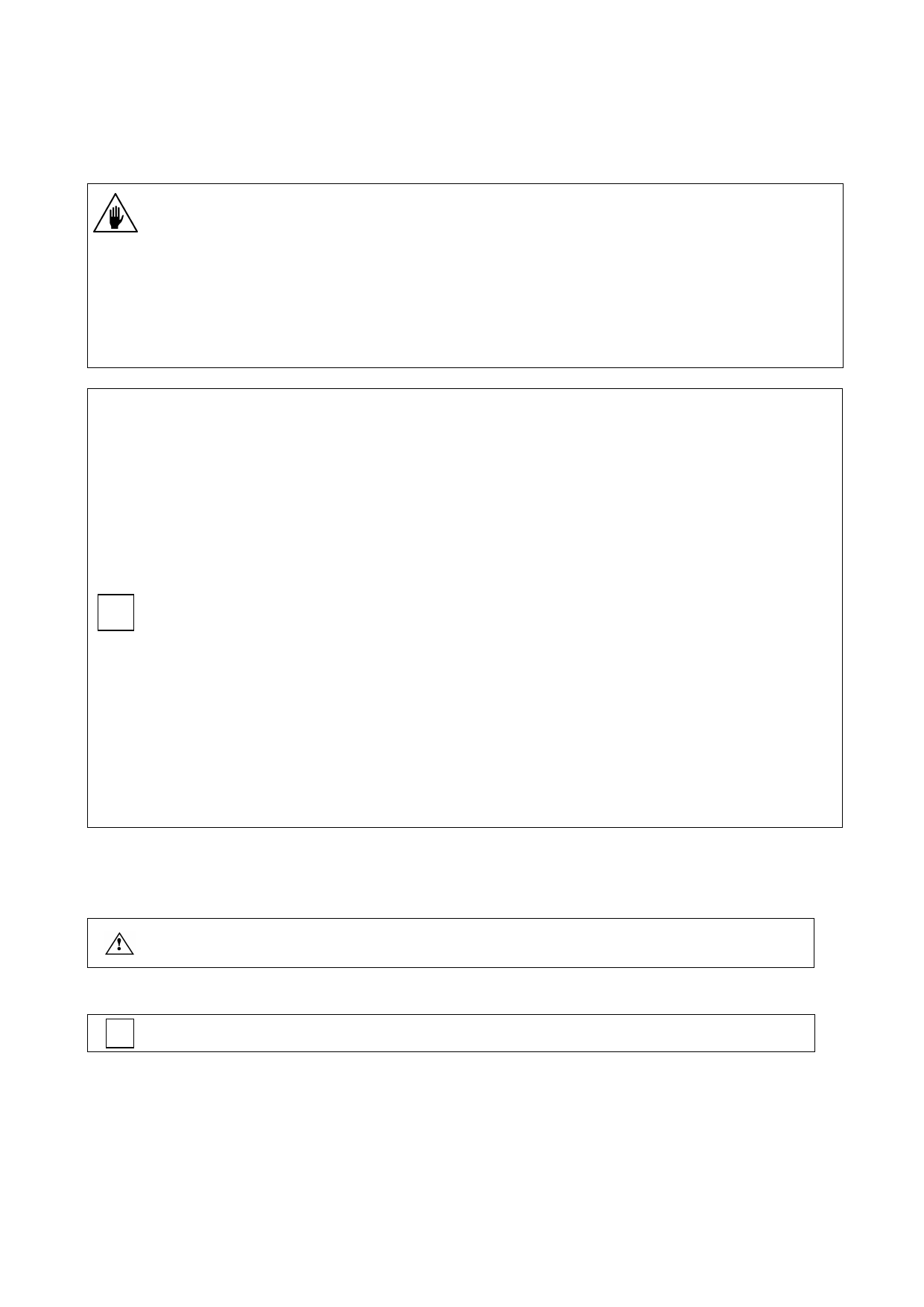
______ HSD __________________________________________________________________________________
6.6 PNEUMATIC AND HYDRAULIC CONNECTIONS
See data sheet
6.7
COMPRESSED AIR SPECIFICATIONS
IMPORTANT :
Introduce compressed air of a purity in accordance with ISO
8573-1, classes 2 4 3, i.e.:
• class 2 for the solid particles: size of the solid particles < 1 µm
• class 4 for the humidity: dew-point < 3°C (37.4°F)
• class 3 for the total oil: concentration of oil < 1 mg / m3
Missing to follow the above mentioned specification might cause damage to the product.
Warranty is denied if pollutant traces are found during servicing.
As an example, a possible implementation of the above mentioned specification could be
made by the following instructions.
• Use nonreturn valve to separate the circuit of the dry air from the circuit of the lubricate
air (if present).
• Install the filters shown in the figure below as near as possible to the electrospindle.
• As filter efficiency is less than 100%, it’s important to feed the compressed air circuit of
the CNC machinery with air properly processed.
As an example, put in point (1) of Figure 6.3 air of a purity in accordance with ISO 8573-
1, classes 7 6 4, i.e.:
i
o Class 7 for the solid particles:
size of the solid particles < 40 µm;
concentration of solid particles < 10mg/m3;
o Class 6 for the humidity:
dew-point < 10°C;
o Class 4 for the total oil:
concentration of oil < 5 mg/m3.
• At the end of the working day, unload the pneumatic circuit, to let the automatic
discharge of the liquids accumulated in the filter cups.
• Service regularly the filters, as instructed by the manufacturers, and replace them as
they lose their filtering capabilities (at least once or twice a year).
6.7.1 INTERNAL PRESSURIZATION
The internal pressurisation pneumatic circuit prevents harmful particles from entering the electrospindle. The air
introduced finds an outlet through the gaps of the front labyrinth, in the area of the electrospindle nose.
The pressurisation air must always be present, even when the electrospindle is stopped and the machine
is switched on. It must also be present during the maintenance and cleaning of the machine, to prevent
dust from getting inside.
With the spindle at standstill, check that there is a uniform outlet of air around the spindle shaft (pressurisation); if this is
not the case, check the efficiency of the pneumatic circuit and the tightness of the connections.
i
For pressurisation air consumption and delivery pressure, refer to the technical characteristics card of the
motor.
Y580100001 rev.03 ____________________________________________________________________ 14