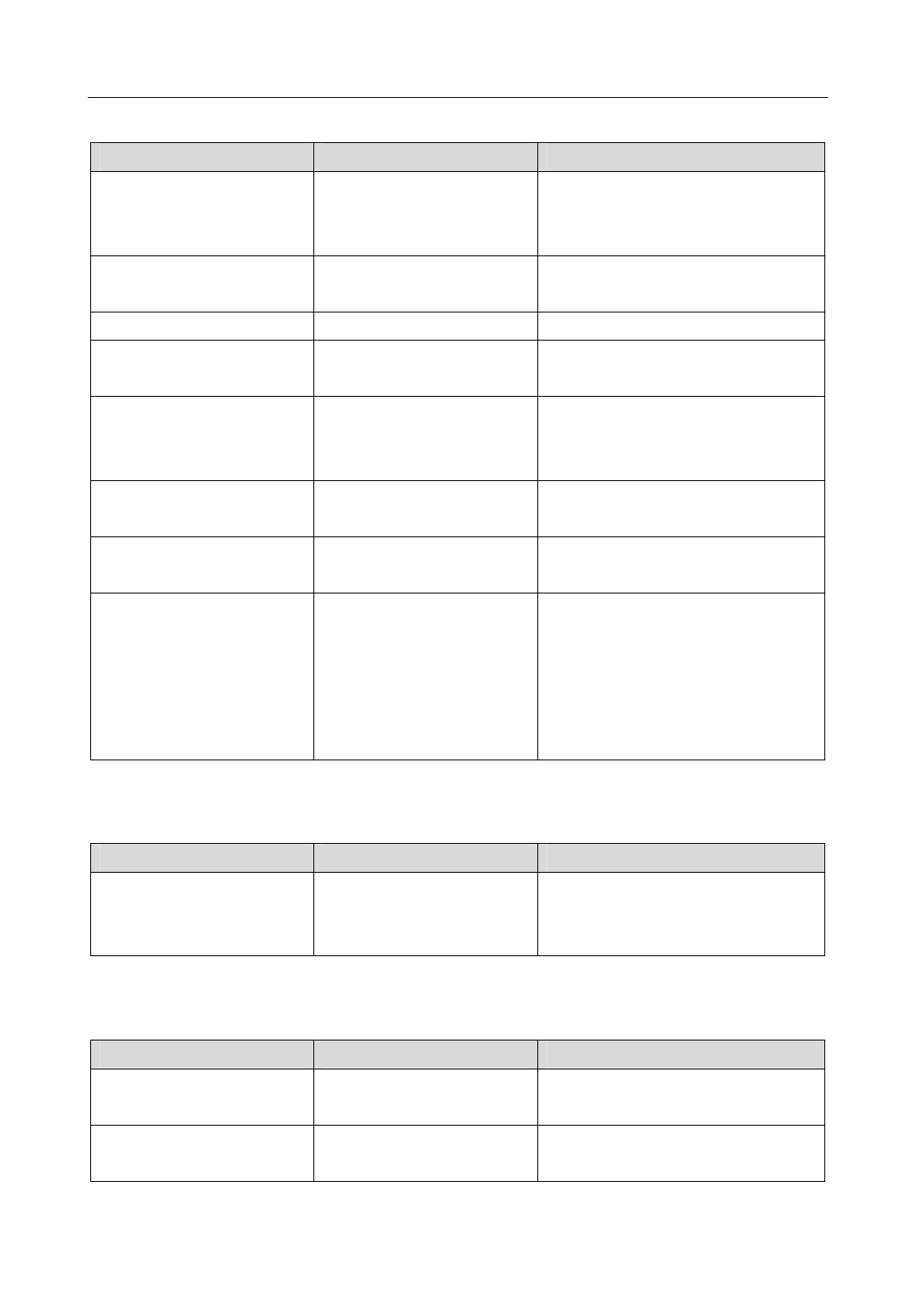
Chapter 6 Alarm
Err 4 (Excess position deviation)
Potential cause
Servomotor U、V、W
connection is not correct
Encoder zero point changes
The encoder wiring error
The servomotor is blocked
The command pulse frequency
is too high
The gain of position loop is too
small
The excess position deviation
range is too small
Torque is not enough big
Check
Check U、V、W wiring
Check the encoder zero point
Check the encoder wiring
Check the servomotor shaft and
its mechanical connection
Check input frequency and the
parameter of
division/multiplication
Check the parameters P009
Check the parameter P079
Check torque
Handle
Correct U、V、W wiring. The U、V、W
must connect with servo driver terminal
U、V、W correspondently.
Install the encoder again and adjust the
zero point.
Correct wiring.
Repair.
z Slow down the input frequency.
z Adjust the parameter of
division/multiplication.
Increasing the gain of position loop.
Increasing the value of parameter P079.
z Increase the torque limit.
z Increase smooth filtering time for
position command.
z Reduce load.
z Replace the servo driver and
servomotor with bigger ones.
Err 7 (Drive inhibition abnormal)
Potential cause
The CCWL and/or CWL
over-travel inhibition is invalid
when servo is on
Check
Check CCWL、CWL wiring
Handle
z Correct input CCWL、CWL signal.
z If not use CCWL、CWL signal can
shield it by setting parameter P097.
Err 8 (Overflow of position deviation counter)
Potential cause
The servomotor is blocked
The command pulse is
abnormal
Check
Check the servomotor shaft and
its mechanical connection
Check command pulse
Handle
Repair.
82