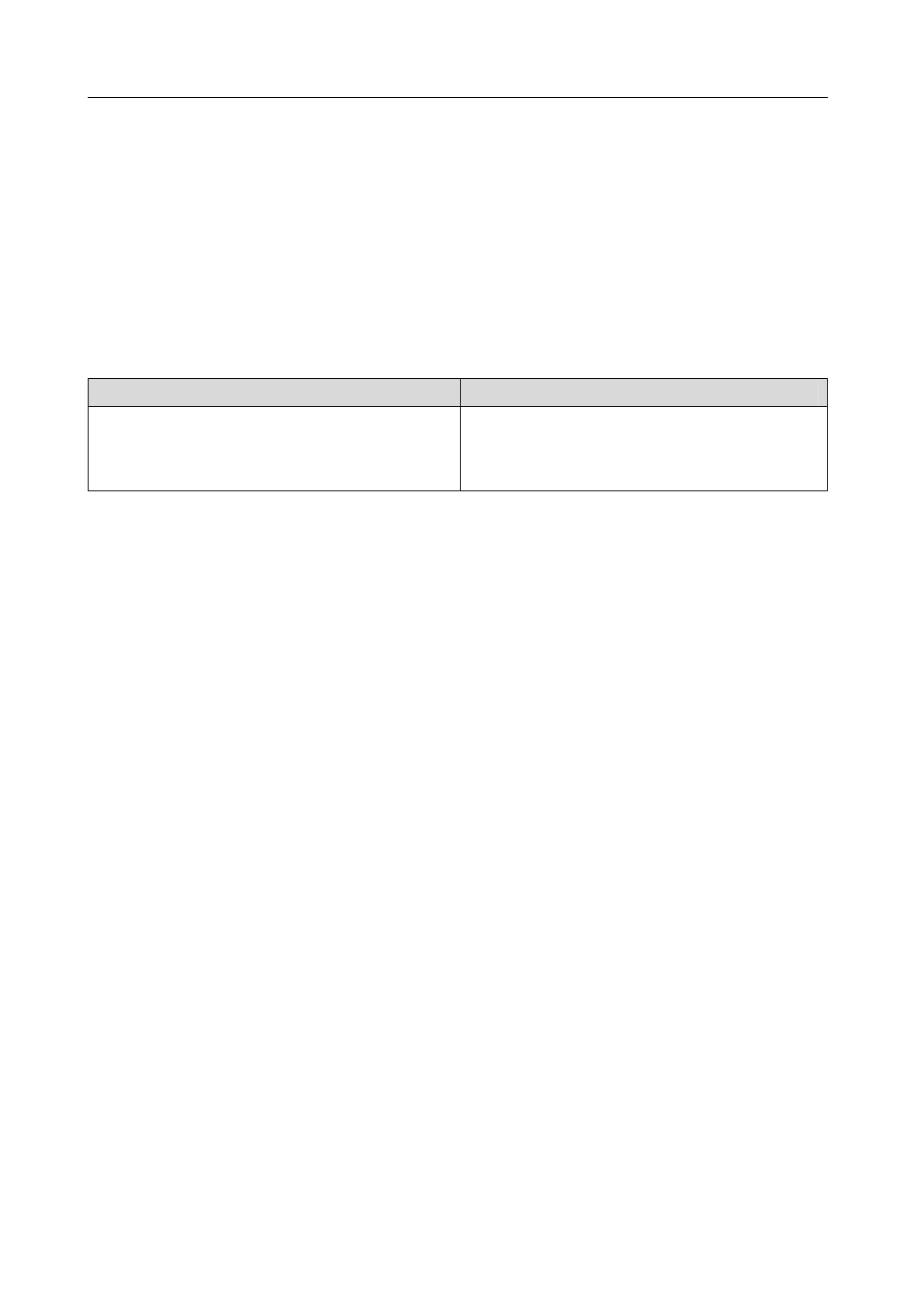
Chapter 4 Running
4.3.2 Procedure for gain adjustment
The bandwidth selections of the position and the speed loop depend on the machinery rigidity and the
application situation. A leather belt conveyer has low rigidity and may set low bandwidth. Machinery with reducer
and ball bearing screw has medium rigidity and may set medium bandwidth. Machinery with ball bearing screw or
linear motor has higher rigidity and may set high bandwidth. If mechanical characteristics are unknown, may
gradually increase the bandwidth until resonating, and then decreases the gain.
In the servo system, if changes a parameter, then other parameters also need to readjust. Therefore, do not
change a parameter far from its original value. About the steps for changing the servo parameter, please observe
the following principle generally:
Increase response
Decrease response,restrain vibration and overshoot
1.Increase gain of speed loop Kv
1. Decrease gain of position loop Kp
2. Decrease integral time constant of speed loop Ti
2. Increase integral time constant of speed loop Ti
3. Increase gain of position loop Kp
3. Decrease gain of speed loop Kv
Gain adjustment procedure for speed control loop
1. Set the load inertia ratio.
2. Set integral time constant of the speed loop with a relatively great value.
3. Under no vibration and unusual sound increase the gain of the speed loop, if vibration occurs then decrease the
gain a bit.
4. Under no vibration and unusual sound, decrease the integral time constant of speed loop, if vibration occurs
then increase the time constant a bit.
5. Because the mechanical system may have resonating factors and is unable to adjust for a bigger gain, then the
desired response cannot obtain. Now, adjust the filter time constant (parameter P007) of torque, and then carry on
above steps again enhancing responsiveness.
Gain adjustment procedure for position control loop
1. Set the load inertia ratio.
2. Set integral time constant of the speed loop with a relatively great value.
3. Under no vibration and unusual sound increase the gain of the speed loop, if vibration occurs then decrease the
gain a bit.
4. Under no vibration and unusual sound, decrease the integral time constant of speed loop, if vibration occurs
then increase the time constant a bit.
5. Increase the gain of position loop, if vibration occurs then decreases the gain a bit.
6. Because the mechanical system may have resonating factors and is unable to adjust for a bigger gain, then the
desired response cannot obtain. Now, adjust the filter time constant (parameter P007) of torque, and then carry on
above steps again enhancing responsiveness.
7. If need shorter positioning time and smaller position tracking error, can adjust the feed forward of the position
loop. Please refer to 4.2.4 section.
48