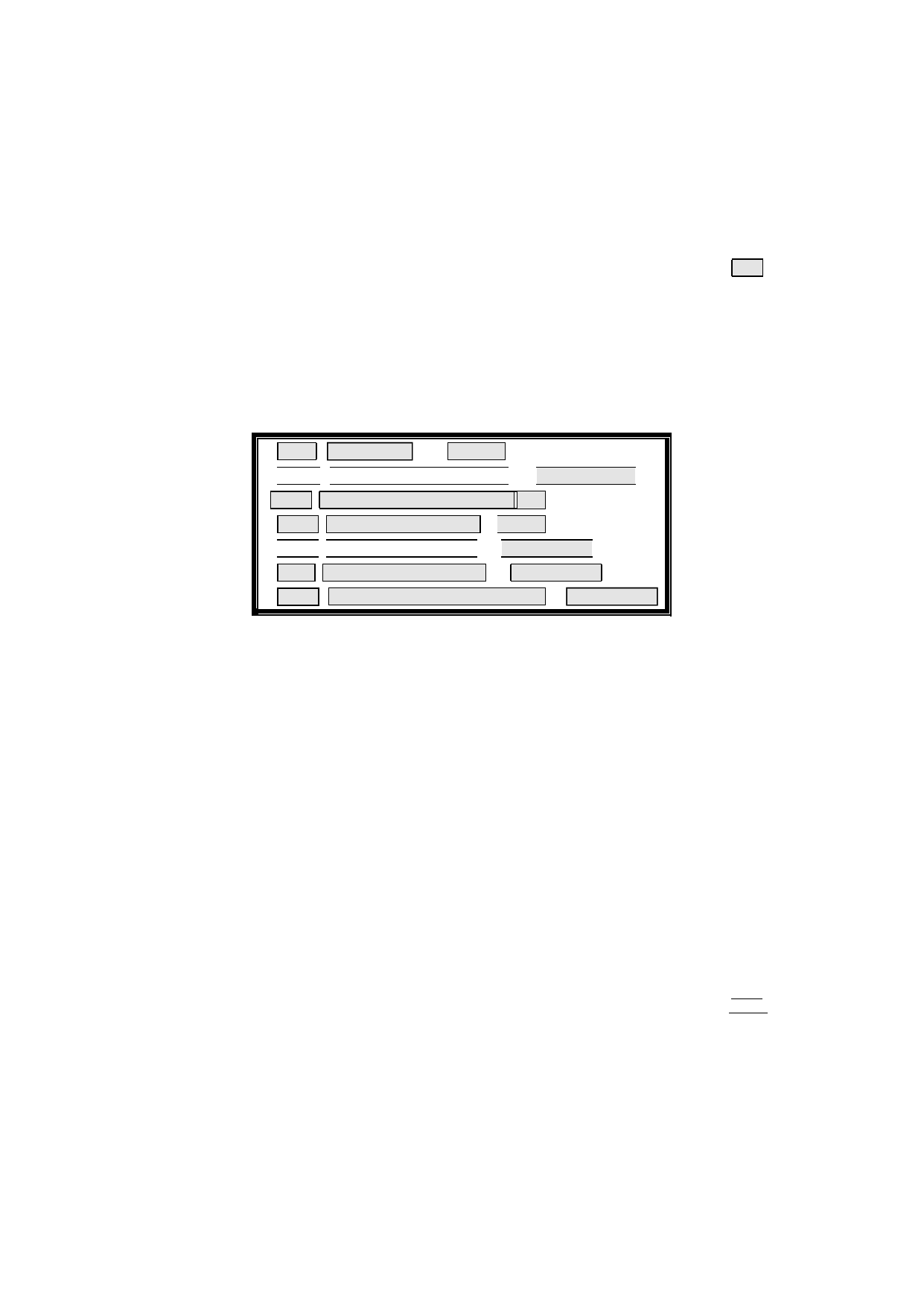
correct.
3. Do not connect the servo enable signal temporarily. Check whether there is any alarm and observe the red
lamp (ALM). If the red lamp is not on, the operation is normally and you can go to the next step.
4. Start the adaptation of parameters.
a. Enter the parameter modification mode to change PA-0 into ― 385 ‖ password and then change
Parameter PA-1 into ―49‖ as the motor type code (see Table 2.2 on Page 8).
b. Enter the parameter management mode ―EE--‖, transfer to ―DP-def‖ and then press down Enter
for three seconds. When ―Finish‖ appears, it means the default value has been restored according
to the current adapted motor and will be effective only after power down.
c. After power on again, check several key parameters (See Table 8.2 below) of speed control and
confirm that they are correct; the upper computer can send out an enable signal (or internal enable), and
send out an analog signal after the green lamp (Run) is on and after automatic zeroing. Observe the
dynamic effect of the motor, appropriately modify the gain and adjust the zero drift value.
PA-- Control mode Set to 1
4–
PA--20--Driver disablement ineffective
Factory value=1
PA-22 –Internal speed command selection Set
PA-40 –Acceleration time constant et as
PA-41 –Deceleration time constant Set as required PA-
Analog speed command gain Set as required
43–
PA-45 -- Analog speed zero drift compensation Set as required
Table 8.2 Adjustment of Key Parameters of Speed Control
Torque Control (Quick adjustment of parameters after power on)
Example: A MG-1000/3A driver matches a 110ST-M06030 motor (torque control).
1. Confirm that the three-phase 220V voltage between R, S and T is correct after power on.
2. Confirm that the wiring of the differential input of the torque analog value or the single-ended input is
correct.
3. Do not connect the servo enable signal temporarily. Check whether there is any alarm and observe the red
lamp (ALM). If the red lamp is not on, the operation is normally and you can go to the next step.
4. Start the adaptation of parameters.
a. Enter the parameter modification mode to change PA-0 into ―385‖ password and then change Parameter
PA-1 into ―38‖ corresponding to the motor type code (see Table 2.2 on Page
8).
b. Enter the parameter management mode ―EE--‖, transfer to ―DP-def‖ and then press down Enter
for three seconds. When ―Finish‖ appears, it means the default value has been restored according
to the current adapted motor and will be effective only after power down.
c. After power on again, check several key parameters (See Table 8.2 below) of torque control and
confirm that they are correct; the upper computer can send out an enable signal (or internal enable), and
send out an analog value signal after the green lamp (RUN) is on and after automatic zeroing. Observe
the dynamic effect of the motor, appropriately modify the gain and adjust the zero drift value.
73