- You are here:
- AM.CO.ZABuythisCNC Utilities Homepage
- TruCUT-CO2-Laser-Machine
- Component Manuals
- 常见 轮廓图提取方法.pdf
- Page 4 of 4
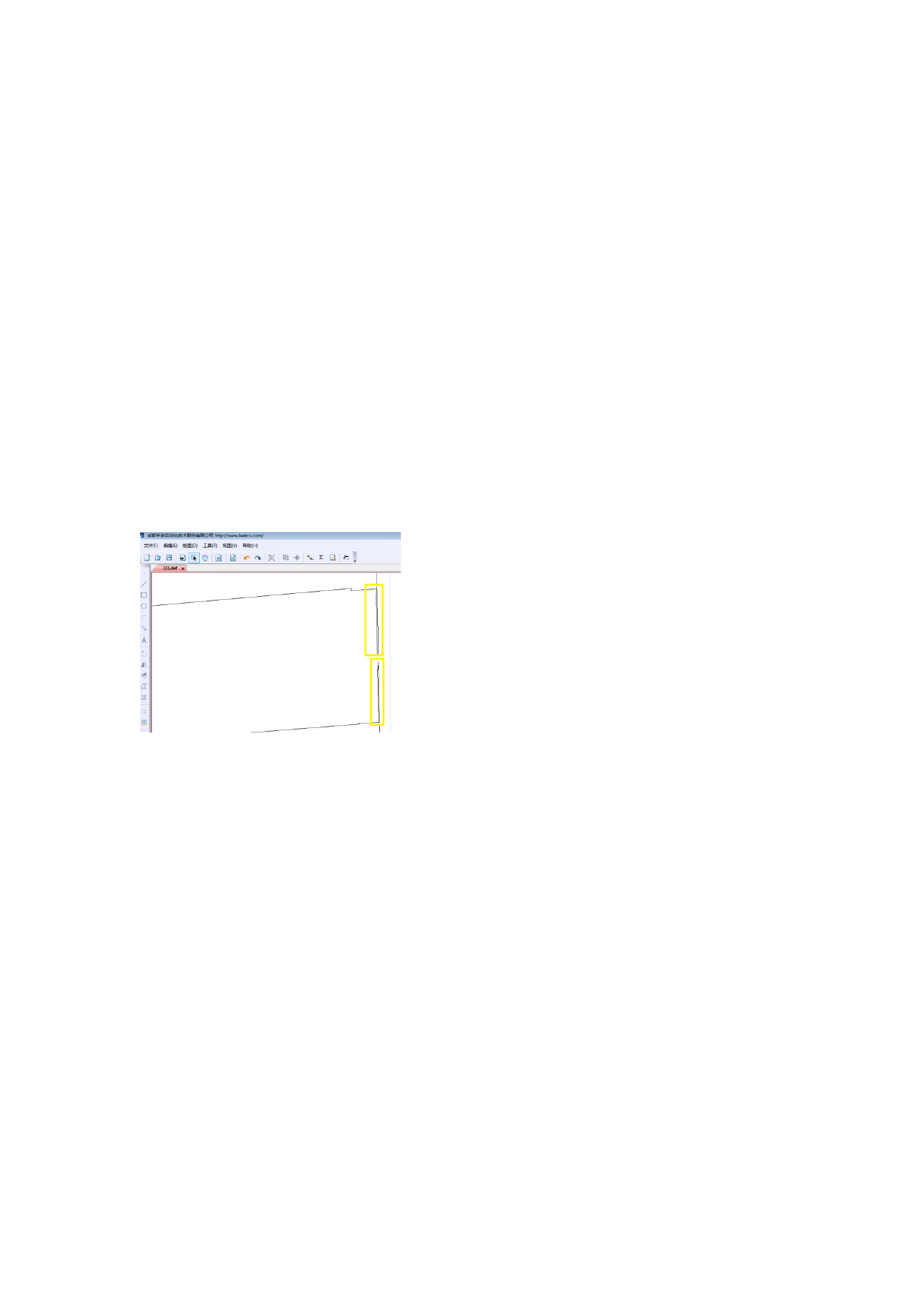
B:第一个 MARK 点正常扫描结束,后续 MARK 点扫描失败
可能原因:
1:MARK 点印刷太小,通常要求宽度要大于 6MM。长度大于 50MM
2:MARK 点印刷实际尺寸与理论尺寸偏差较大
3:板材翘曲严重或者设备高度安装不合理,正常要求在 10MM 正负偏差 2MM
4:摆放切斜角度过大
解决办法:
1:观察在后续 MARK 扫描过程光线是否正确进入黑色区域和白色区域以及进入黑色区域和
白色区域是否指示灯为量和灭,如果量灭不正常,请重新在不正常的 MARK 点已该 MARK 点
未基准进行重新颜色校准,导致该问题的原因为 MARK 点印刷各个点颜色差异或者底色差
异导致。
2:如果板材翘曲严重和平台台面严重不平整,需要进行设备调试和板材固定。
C:实际加工中出现一些异常轨迹
可能原因:
1:提取轮廓图异常,需要在导入加工前对轮廓图进行人工处理,如下图,实际黄色框选区
域加工过程不希望激光切割,但是实际轮廓放大看到此处存在折线,因此实际加工此处会认
为是异常轨迹。
解决办法:
1:提取轮廓后如果发现有异常,需要在第三方软件上进行轮廓图的预处理。
D:实际加工中出现轮廓偏差
1:实际印刷过程比如亚克力存在正印和反印等场景,如果正印切割轨迹完全正确,可能出
现在反面印刷切割出现偏差,需要再次对偏移量进行微调,此种现象是亚克力透光性导致的,
同种印刷工艺轮廓切割是完全正确的。
2:4 个十字标的中心不能组成一个矩形,即在水平方向和垂直方向未完全对齐;要求在作
图的时候需要使用作图工具对齐,不能仅凭肉眼观察平齐。
3:4 个十字标印刷的时候不在加工图像的 4 个边角位置。
4:在将偏移量调整试切完全正确的情况下,需要在机器设置中执行一次写参数操作,以便
再次重新安装软件后,直接执行读参数即可正确使用设备。
5:在整版切割中(1200*2400)切割中发现前面几排切割是准备的,后面慢慢出现偏位现象。
可以采取以下方式验证,可以在整版加工中先试切一个对角的图形(比如左下一个右上一
个),如果这个两个图形切割是准备的,说明机器的参数以及精度都是完整正确的,在整版
加工过程中出现偏差原因为亚克力板在加工过程中由于设备抖动以及抽风机以及吹风等等
因素导致切割过程整版材料发生了位移导致的,可以采取机械雕刻机的方式适当采取一些工
装将材料进行固定,以达到最理想的状态。