- You are here:
- AM.CO.ZABuythisCNC Utilities Homepage
- EasyRoute-CNC-Router
- Italy HSD Spindle
- Y580100001_AT-MT_en_Rev 04.pdf
- Page 18 of 22
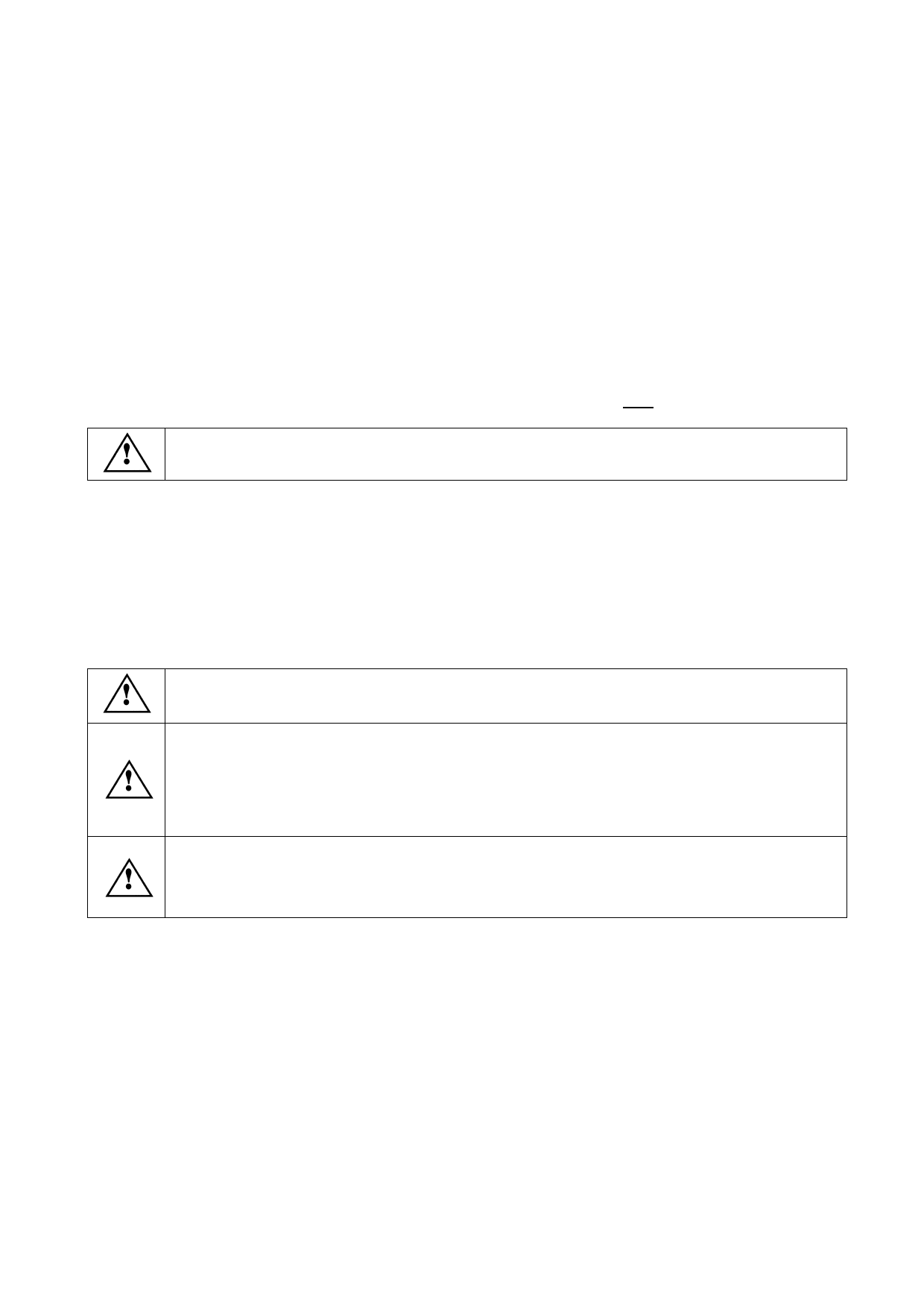
______ HSD __________________________________________________________________________________
8.3 CHOOSING TOOLS
8.3.1 TOOLS
Bear in mind the following recommendations when choosing tools:
a) Only use fully sharpened tools, and make sure that they are securely locked in the spindle.
b) Never use bent or damaged tools, chipped tools, or tools that are not perfectly balanced.
c) Always make sure that the mating surfaces of tools are perfectly clean and dent free before fitting the tool in the tool
holder.
d) Never use tools at speeds in excess of that punched on them or specified by their manufacturer.
e) Always ensure that the following essential requisites are met before using any tool at high speed:
• The tool must be of compact, short, and lightweight design.
• The tool must be a precision instrument, and any inserts must be held in to a high degree of security.
• The tool must be balanced and must mate symmetrically with the tool holder.
• The cutting surfaces of the tool must be located near its centre of rotation.
In general, the recommended balance rating for tools run at speeds over 6000 RPM is G2.5 (ISO 1940 standard).
UNLESS OTHERWISE REQUESTED BY THE CUSTOMER, ELECTRO-SPINDLES WITH TOOL ENGAGEMENT KEY ARE
BALANCED WITH THE KEY IN PLACE. (SEE DATA SHEET.)
Because of the many factors to consider, it is not possible to summarise in table form the diameters and maximum
weights of tools for any specific speed.
For all special applications, customers should ask HSD’s Technical Office to perform theoretical calculations using their
special calculation software.
Final analysis must always be performed on the machine itself, with the tool correctly fitted, and at the normal operating
parameters. Operating vibrations must be measured on the electro-spindle at the points defined in conjunction with the
H.S.D. Technical Office.
MAXIMUM PERMISSIBLE VALUES FOR VIBRATIONS MEASURED ON ELECTRO-SPINDLES MUST FALL WITHIN CLASSES I-
K ACCORDING TO ISO 2372 - VDI 2056 STANDARDS.
ALWAYS CHECK THE MAXIMUM OPERATING SPEED OF TOOLS. THIS IS EITHER PUNCHED ON THE TOOL ITSELF OR
OTHERWISE SPECIFIED BY THE TOOL MANUFACTURER.
DURING MACHINING, TAKE GREAT CARE TO AVOID CONTACT BETWEEN NON-CUTTING ROTATING PARTS (SPINDLE
SHAFT, TOOL RING NUT, ETC.) AND THE WORK. ACCIDENTAL CONTACT CAN LEAD TO DAMAGE TO THE ELECTRO-
SPINDLE OR INJURY TO THE OPERATOR.
NEVER START ELECTRO-SPINDLES FITTED WITH TOOL ENGAGEMENT KEYS WITHOUT A TOOL IN PLACE AND
CORRECTLY TIGHTENED IN THE TOOL HOLDER.
WITH AT SERIES ELECTRO-SPINDLES IN GENERAL, THE BEARINGS OF BOTH SUPPORTS ARE ELASTICALLY PRE-
LOADED TO ELIMINATE THE AXIAL PLAY FROM THE RADIAL BEARINGS AND TO REDUCE VIBRATION AT HIGH SPEED.
IF, DURING MACHINING, THE SPINDLE SHAFT IS SUBJECTED TO A FORCE OPPOSITE TO AND IN EXCESS OF THE PRE-
LOADING FORCE, THE SHAFT CAN MOVE AXIALLY FOR A VALUE EQUAL TO THE AXIAL PLAY IN THE BEARING, AND
VIBRATIONS CAN INCREASE ACCORDINGLY.
Y580100001 rev.03 ____________________________________________________________________ 18