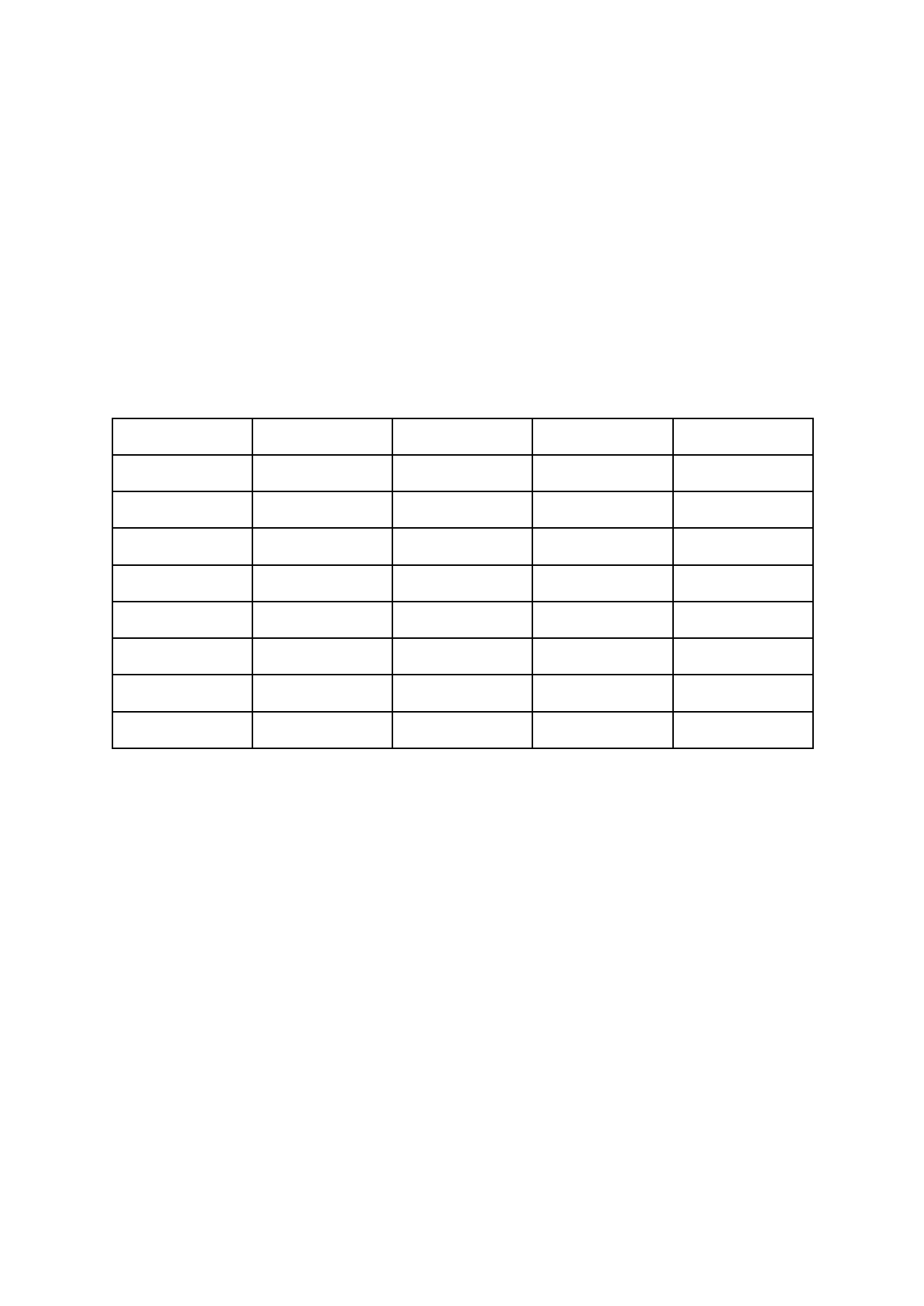
How to check and/or adjust the settings on Easy Route ATC servo
motor drives.
1. Press set button
2. Press mode button until you come up to PA000 settings
3. Using the arrow keys select the PAxxx setting you want to check and press set. The
current setting will be shown and to adjust it use arrow keys then press set.
4. Repeat for all PA settings below.
5. Once done with all press mode repeatedly until you get to d0ISP and press set.
6. Reboot the CNC router for settings to take effect.
Default settings for ATC servo motor drives.
Setting
PA000
PA002
PA003
PA006
PA007
PA400
PA009
PA010
X
100
1
14
0
3
83
62144
1875
Y1
100
1
14
0*
3
83
62144
1875
Y2
100
1
14
1*
3
83
62144
1875
Z
100
1
14
0
3
83
32768
125
PA000 - Three axis synchronisation parameters ensure that when a job is running all 3
axes are in sync according to the instructions from the GCODE enabling precision and
accuracy of the work. In other words the motion of the axes is synchronised such that all the
axes start and stop moving simultaneously, and at any point during the move, each axis has
completed the same percentage distance (or ratio) of its move.
PA003 - Motor rigidity is the ability of the motor shaft to resist external torque interference.
We can adjust the rigidity of the motor in the servo driver. The mechanical stiffness of servo
motor is related to its response speed
PA004 - Motor inertia ratio in servo-driven systems, can be used as a measure of how well
the motor is able to control the acceleration and deceleration of the load. Inertia ratios are
typically given for stepper or servo motors, and they are calculated by dividing the total
amount of load inertia (or reflected load inertia if geared) by the rotor inertia of the motor. If
these values are exceeded, the motor may miss steps, stall, or vibrate.
PA006 - Motor direction is determined by the pulse sent to the motor, in essence servo
motor control of the shaft position comes from using a pulse width modulation signal (PWM)