- You are here:
- AM.CO.ZABuythisCNC Utilities Homepage
- FastCOLOUR-Printer
- How Inking System Works.pdf
- Page 2 of 13
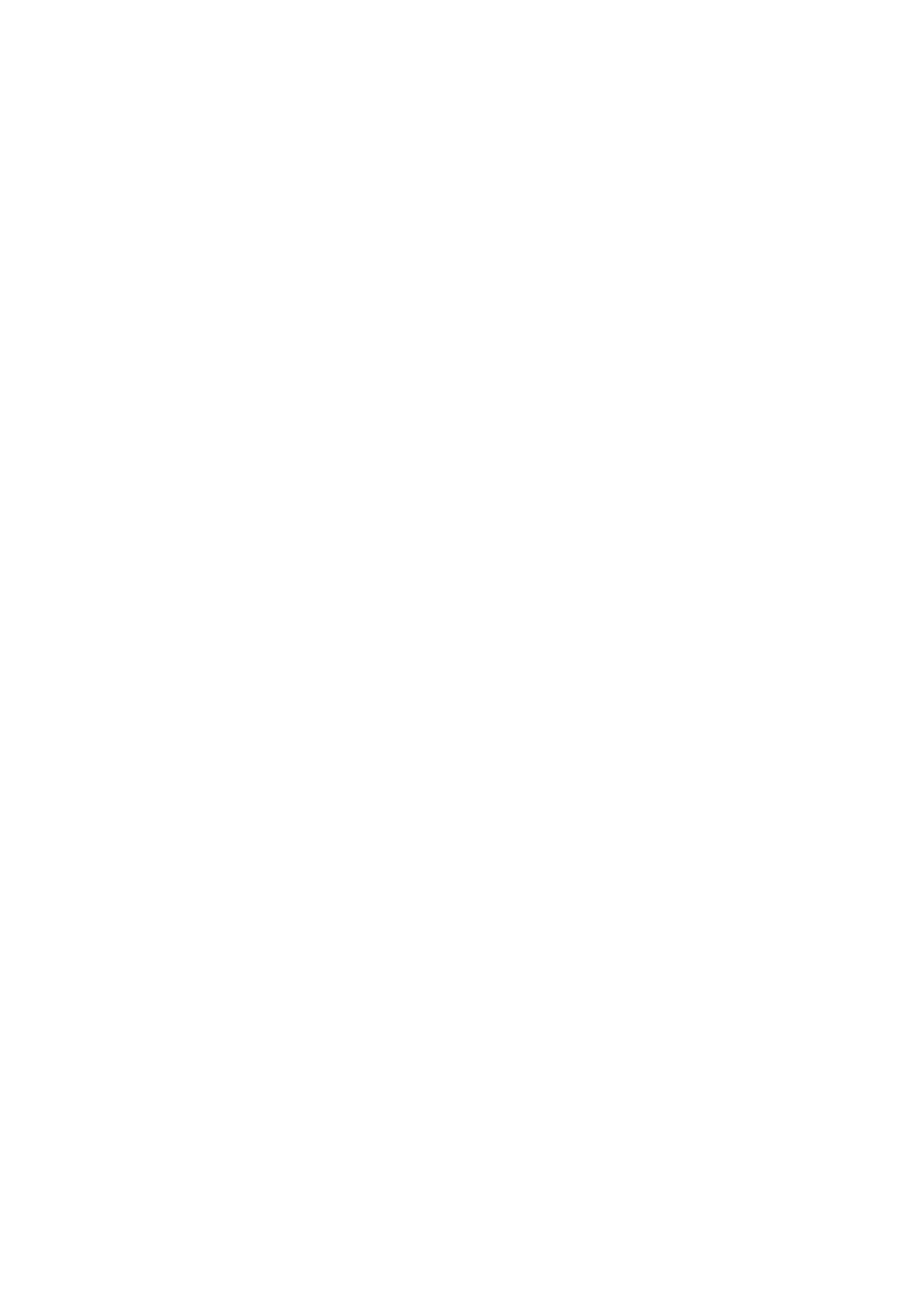
Processing) software process the printing file, knows which
colour is from where.
Once ink left printhead by whatever means, the space that was
occupied by the ink became a vacuum , therefore the ink
started to flow from the Damper into the printhead, and since
the pressure inside damper drops too, the ink from ink tank in
the back of the machine starting to flow and refill the damper.
The ink in the damper always around half full because the air
inside the damper will prevent it from being too full. When it's
very full, it won’t act as a flow controlling device.
When the printhead does not print, we will cap the printhead to
prevent ink from drying ensuring that it does not have any
contact with the air or lights especially for the UV ink. Our ink
capping device consists of two parts. The first one is an Ink
Cap, which is a square shape that matches the printhead
surface with a rubber seal. Underneath the Printhead is 1 or
more outlet for tubes to move ink away. There will be
mechanical or motorised structure to move the ink from cap to
cap to the printhead when needed, we call this the ink cap
station.
The tubes that connect to the cap will connect to an ink pump.
This is used to pull the ink from the ink cap itself as well as
from the printhead if capped. The ink that is pulled out will be
sent to a bottle to store waste ink that is there.
The ink starts flowing from the ink tank at the back of the
machine, and then gets pulled by pressure applied through the
tubes all the way to the damper, inside the printhead. The Ink is
either sprayed out by printhead onto printing media, or pulled