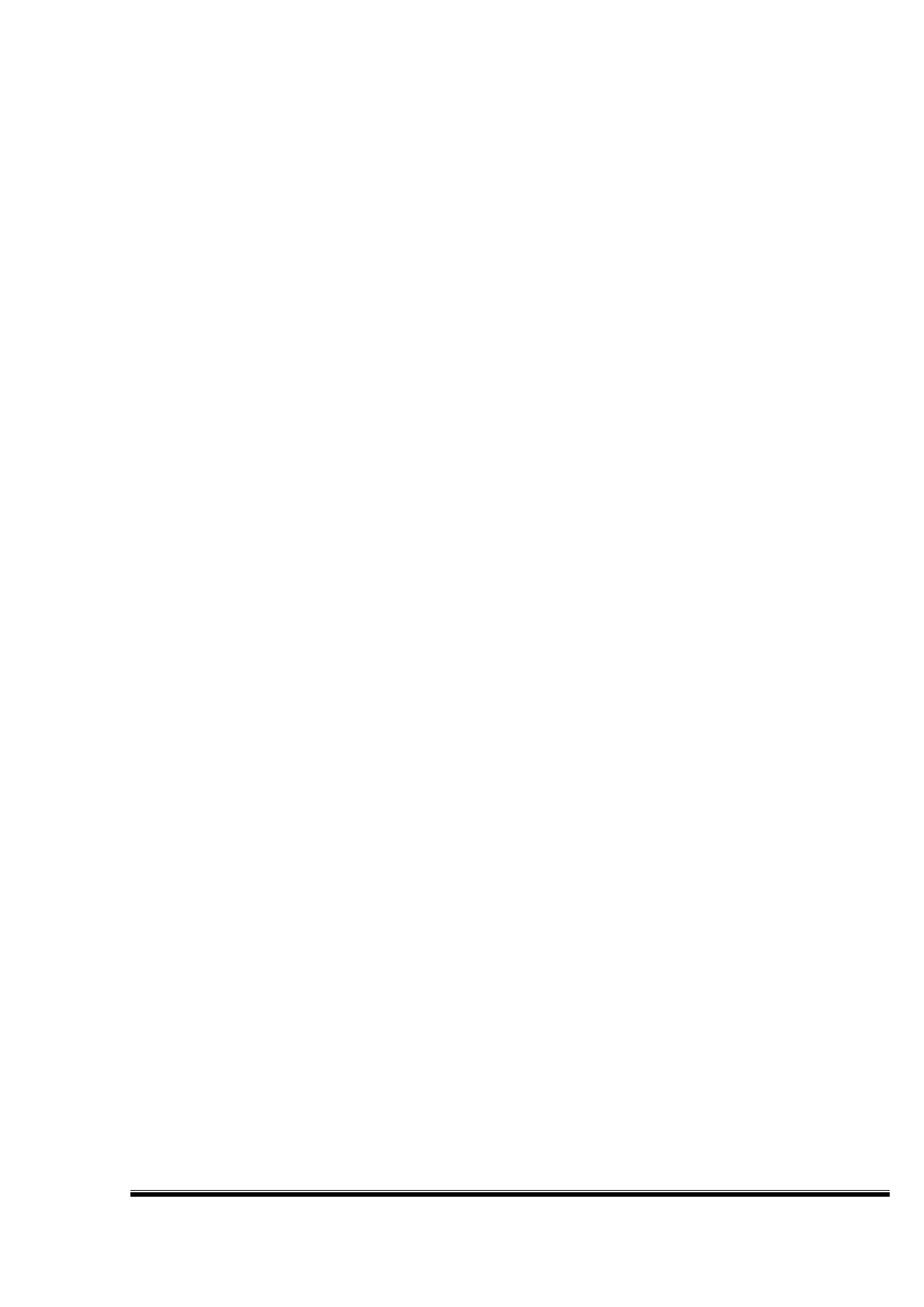
Chapter VIII Operation Procedure
1. Preparation for Equipment Commission:
1) Open the package and check the fittings are consistent with the accessory list.
2) Remove the transport fixture ,push the gantry back and forth, check Y-axis movement is
normal, and then push the car right and left , check the X- axis movement is normal.
3) Install the vacuum sucking pump: connected the inlet hose of the vacuum sucking pump
with the steel soft wire , and then the other end connect to the suction valve at the port.
4) Preparation work : a: to prepare the ink sac ,cut the soft ink tube 16 piece about 10cm in
length, and put copper screws and washers , insert the hose into the ink sac and tighten the
copper screw , connect the three-way with 2 ink sacs; b: install the control software and Rip
software . Fill the ink : put the ink tube into the ink bottle , ink bottle tube head to the bottom
of the lowest , the ink in the ink bottle tube can not bend.
5) Ink supply board powered : after fill the ink, the supply board will energize , followed
connect the float signal lines of the secondary ink tank to the ink supply board one by one,
when a secondary ink tank is full and then to fill the next color.
6) Install printhead: insert the printhead line into the printhead correspondently, contacts can
not have tilt, skewed, and connect the upper line to the UP side on the spray car plate
inserted and the lower line to the DOWN side.
Prohibit: Never use another liquid, especially water-based and solvent cleaning fluid
to clean the nozzles, otherwise will damage the nozzles.
2. Debugging Process:
1) Hardware debugging:
a, Connect the power: after connect the power, connect the USB data cable into your
computer, install the device driver.
b, Open the software, and make the X-axis motor calibration, open the software and rise
the gantry to the highest goal, in the "Settings" "Basic parameters" to make the X-axis motor
calibration, "move", "Reset" three times, in "gear ratio, "the first three digits unchanged.
c, Adjust the ink stack height: after Close the software, under the software installation
directory folder, modify the move out pulse number consistent with the return pulse of the
wiper, and the return pulse number is bigger than the move out one, until the wiper can
clean off all ink residue; adjustable the pulses number of ink nozzles in the cleaning
process. When cleaning the nozzles, they should be close together to prevent ink leakage.
d, With a clean syringe inserted in the ink tube, suck out the ink, and then connect the three-
direct with two ink sac, pumping on the ink sac ink, the ink sac vertically inserted in the
nozzle, no leakage; or insert the ink tube into the sac, and then insert the ink sac into the
nozzles, with the pumping ink button to pump out the ink.
2) Printhead Calibration:
After the nozzle height adjusted, print head status to ensure normal ink drop, and print
vertical alignment, firstly adjust the physical location of the left head, and then the physical
location of the right head. Print the head status to see if there is overlap or gaps, adjusting
第 73 页 共 89 页