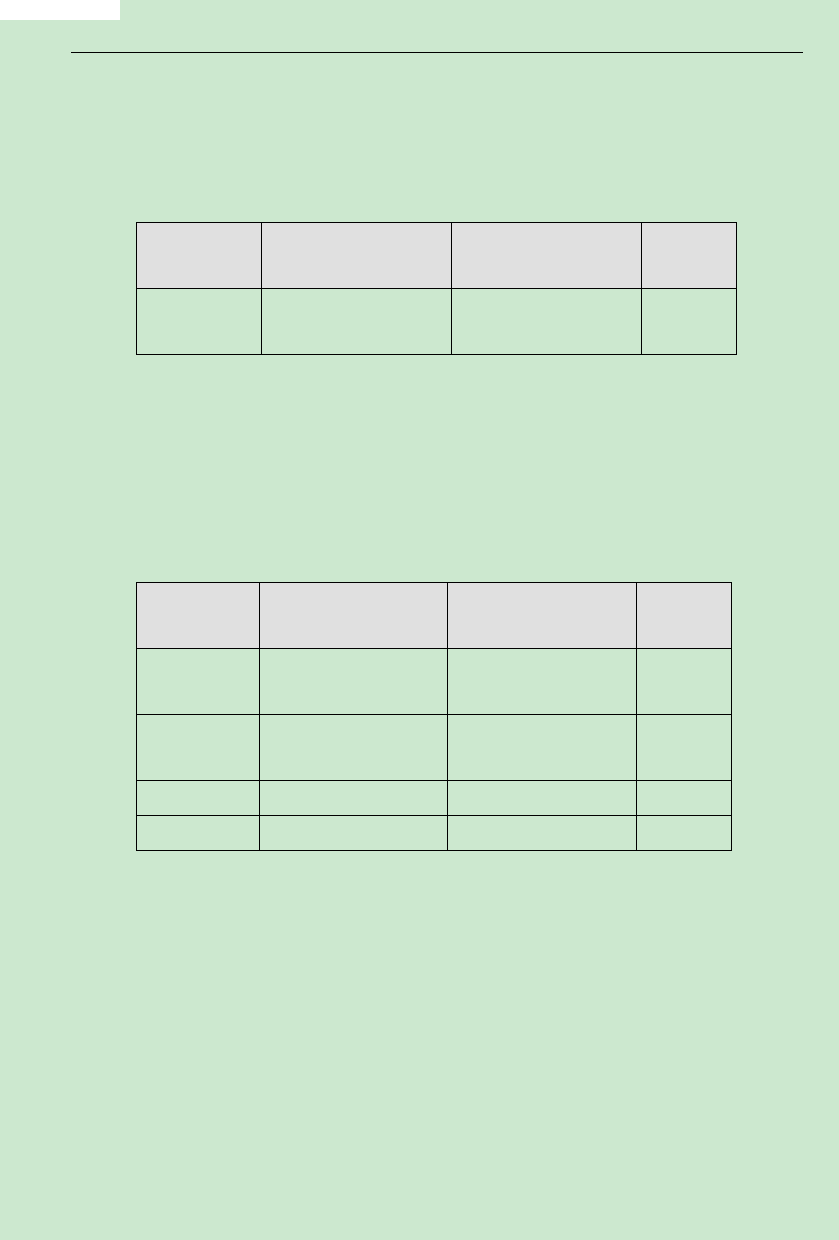
ACD320 user manual
Parameter Description
When it is being started, the inverter first performs DC braking according to the set
prior-to-starting DC braking current, and after the set prior-to-starting DC braking time is passed
then begins to perform acceleration. If the set DC braking time is 0, DC braking is invalid.
The bigger the DC braking current, the greater the braking force. The prior-to-starting DC
braking current is the percentage of the rated inverter current.
Function Code
Name
Setting Range
Default
Value
F0.19
0: DECELStop
Stop Mode
0
1: FreerunStop
0: Deceleration stop
After the stop command is enabled, the inverter decreases the output frequency according to
the Decelerationmode and the definedAcceleration /Deceleration time, and the motor is stopped
when the frequency is 0.
1: Free-run stop
Once the stop command is valid, the inverter immediately ends the output. The loading is
freely stopped by its mechanical inertia.
Function Code
Name
Setting Range
Default
Value
F0.20
Beginning Frequency of
braking
0.00~F0.04
0.00Hz
F0.21
Waiting time of
0.0~50.0s
0.0s
braking
F0.22
DC braking current
0.0~150.0%
0.0%
F0.23
DC braking time
0.0~50.0s
0.0s
Beginning frequency of DC brake when stopping.During the Deceleration stop, when this
frequency is reached, the DC brake is started.
Waiting time of DC brake when stopping: Prior to the DC brake, the inverter blocks the
output, and after this delay time, the DC braking is started. It is used to prevent over-current fault
caused by DC braking at high speed.
DC brake current when stopping: indicates the applied DC brake energy. The bigger the
current, the stronger the DC brake energy should be.
DC brake time when stopping: the durative time that the DC brake energy is applied. If the
time is 0, DC brake is invalid, and the inverter stops the motor based on the set Deceleration
time.
- 62-