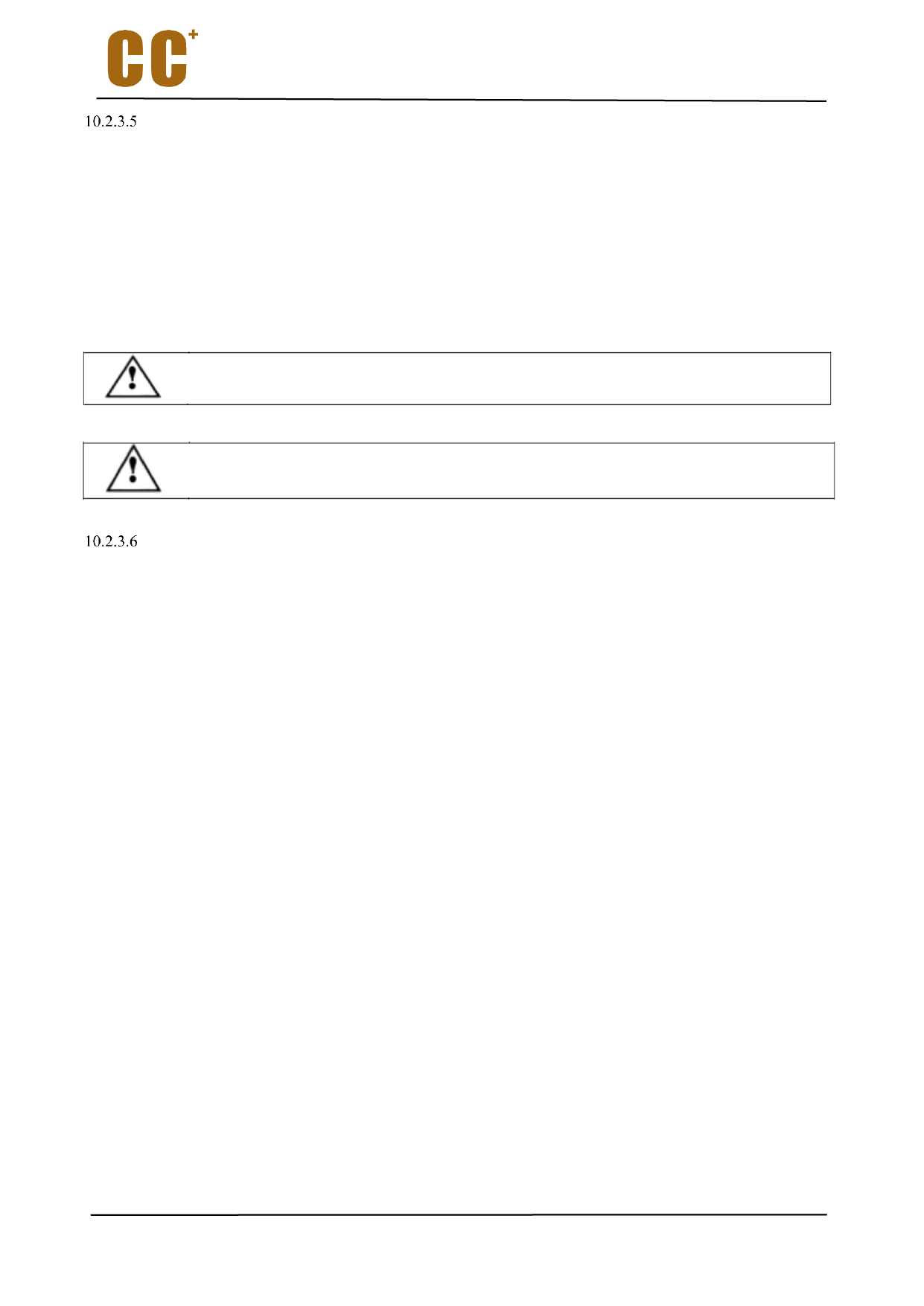
Replacing the sensor unit
1) Remove the screw (6) that blocks the bracket (5) of the sensor to be replaced (4).
2) Unthread the faulty sensor unit from its seat, and disconnect its electrical connector (1).
3) Connect the electrical connector of the new sensor unit. Position the replacement sensor in the empty
seat.
4) Reposition the bracket (5) and tighten the screw (6) without blocking it completely, so that the sensor
can rotate, allowing the calibration operations described in the following paragraphs.
5) After calibration, tighten the screw, blocking the sensor with an open-end spanner so as to maintain the
calibration carried out.
To check the effectiveness of the adjustment, perform the maximum possible number of
tests with all the tool-holders available.
Warning: an incorrect calibration of the sensors can cause irregularities in the
functioning of the electrospindle.
Calibration of the sensors S1, S2 and S3
After replacing the sensor in accordance with section 10.2.3.5, calibrate it as the following steps:
1) Check whether the signal output of the sensor meets the requirements.
2) if not, please rotation sensor bush 4) until it reaches the required output. Keep the sensor in this position
and tighten the screw 6).
10.2.3.6.1 Calibration for S1
When you have replaced the sensor in accordance with section 10.2.3.5, follow these steps to calibrate:
1. Insert the tool-holder cone and ensure that the output of S1 is "ON" if the output is “OFF”, rotate the
sensor unit until it becomes “ON”;
2. Rotate the bush slowly in the direction that takes the sensor away from the tool-holder; stop immediately
when the output of the sensor becomes ”OFF”;
3. Carefully rotate the bush back by about 15° - 20°, so that the output of the sensor returns to“ON”;
4. Rotate the shaft manually, and check that the signal remains “ON” for the whole rotation;
5. Tighten the screw (3);
6. Unhook the tool-holder by powering the cylinder, and check that in this condition (collet open) the output
of S1 is “OFF”;
7. by means of the cylinder, let the collet close without a tool-holder: in this condition, the output of S1 must
be "OFF" for the whole rotation of the shaft;
8. If points [6] and [7] are not satisfied, repeat the procedure from the start, making an even slighter rotation
movement at point [3];
9. If points [6] and [7] are satisfied, make a cycle of 10 tool changes;
10. At the end of the cycle, check that the conditions in the following table are satisfied;
11. If the conditions of the table are not satisfied, repeat the procedure from the start;
12. If the conditions of the table are satisfied, perform a cycle of 100 tool changes with the machine, using
the maximum possible number of different tool-holders;
39