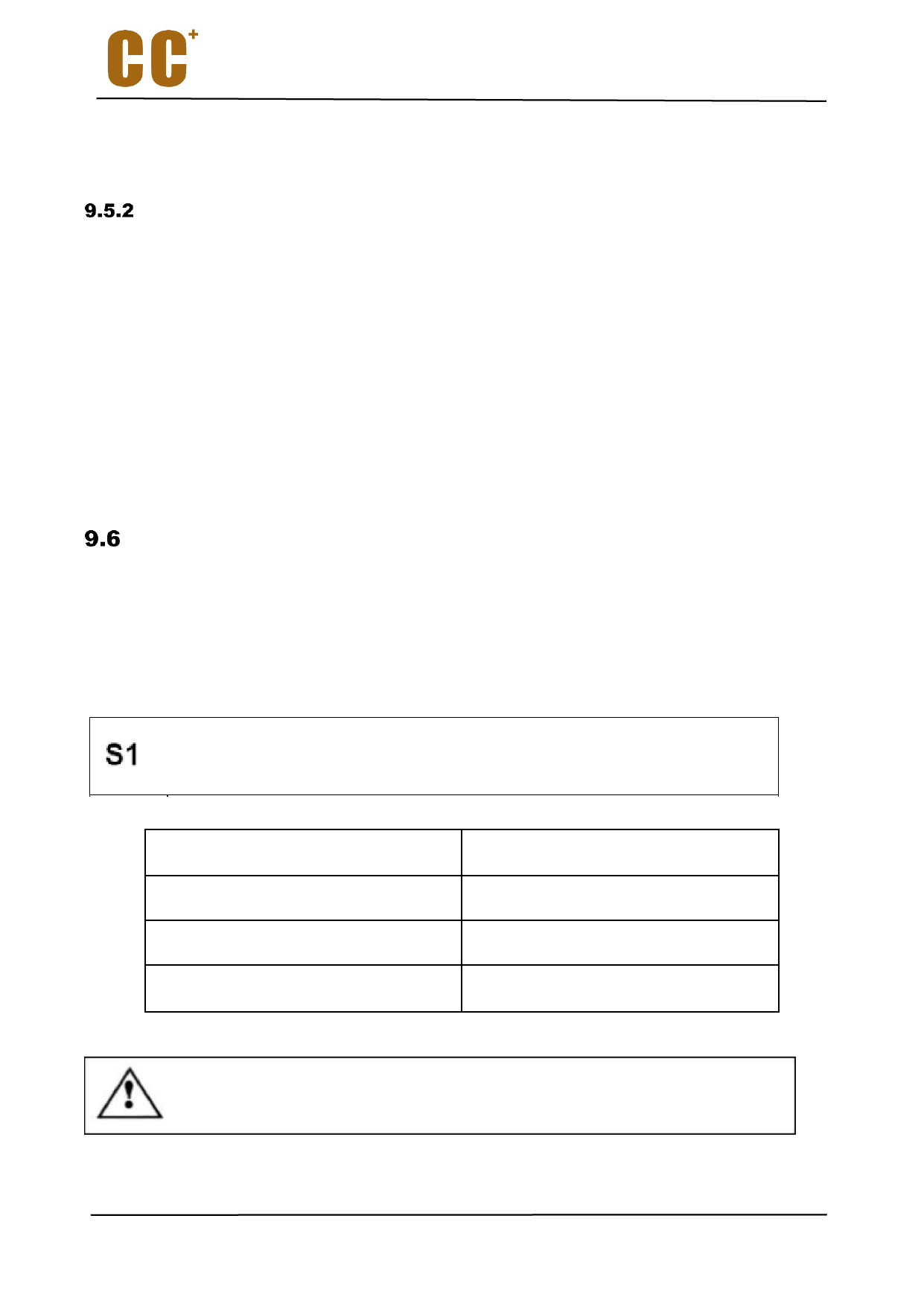
The chart is approximate, in that they do not take into account (because CCMOTOR cannot know this
information) of the machining operation parameters, the specific characteristics of the tool used by the
customer, or the particular type of material being worked: it is the user's responsibility to evaluate
each time the maximum speed that allows him to work safely.
PROCEDURE FOR READING THE CHARTS
(1) On the basis of the distance “X” between the spindle nose and the center of gravity “G” of the tool+tool
holder assembly, choose one of the curves. If the “X” measured on your electrospindle does not
appear on the chart, choose the curve associated with the “X” that is the next measurement bigger
(see example).
(2) Corresponding to the weight of the tool+tool holder assembly, read the value of the maximum speed.
EXAMPLE
On ISO 30 SHORT NOSE, you want to use a pack of milling cutters with the distance “X” between the
spindle nose and the center of gravity “G” of the tool+tool holder assembly 80mm and overall weight
3.5kg(including ring nut and an elastic collet):
(1) With no specific curve for “X”=80mm, it is necessary to refer higher value curve associated
(2) Corresponding to the weight of 3.5kg, you can read the maximum speed, when empty, of 12000 rpm.
SENSORS
Note:
The shaft stop sensor of the electrospindle is optional. This section only describes the sensors for basic
configuration.
For basic configuration the electrospindle is equipped with two sensors: sensors S2 and S1, they are used
for the following functions.
S1 is used to detect if tool holder is attached providing safe signal for shaft rotation.
Condition
Output S1
The tool holder is locked
十 24V
No tool holder
0 V
The tool holder has ejected (open collet)
0 V
Monitor the S1 signal any time the electrospindle is rotating. If the S1 is reduced to 0V, stop rotating.
Monitor the S1 signal any time the electrospindle is rotating. If the S1 is reduced
to 0V, stop rotating.
29