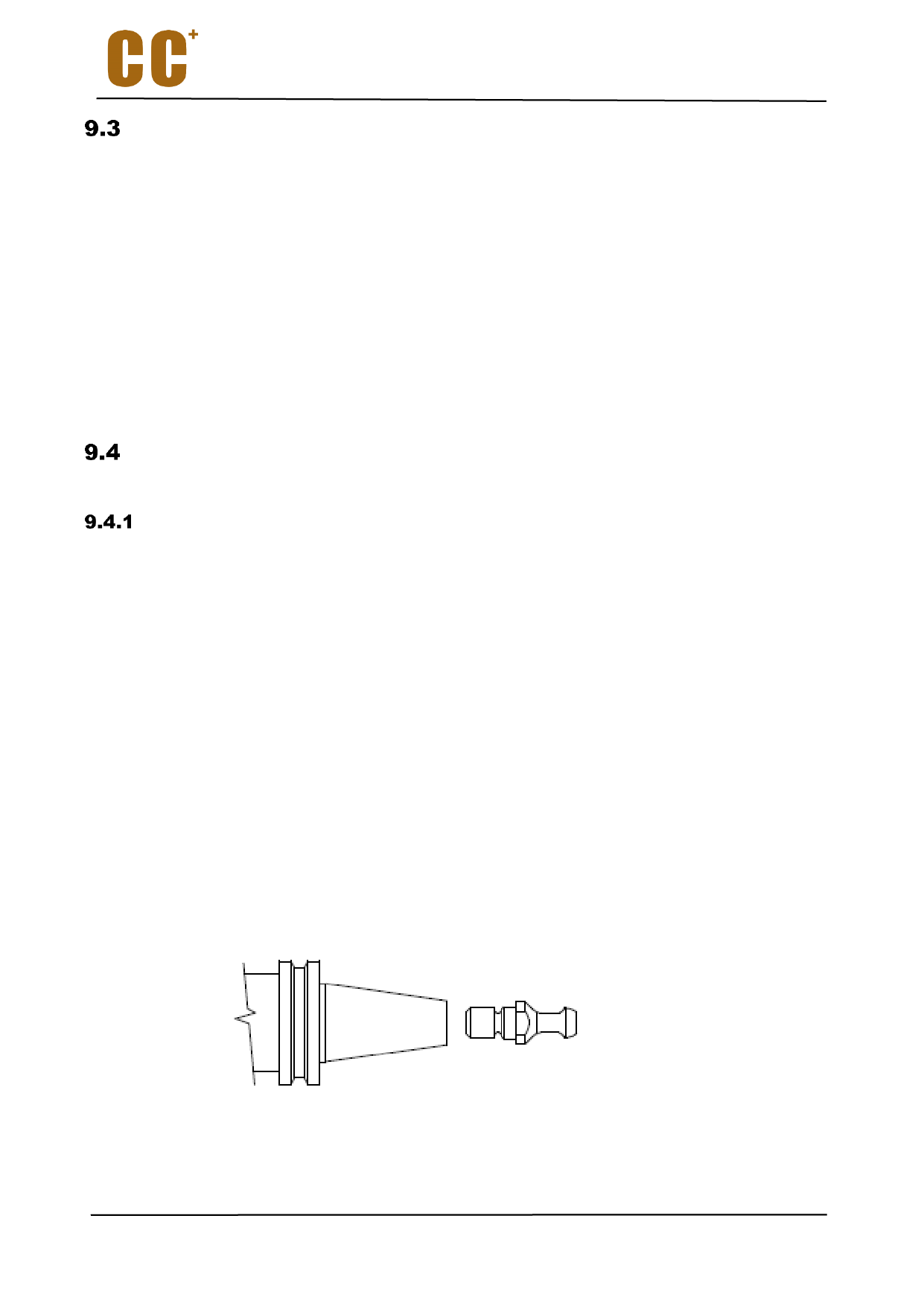
WARM UP
CCMOTOR uses high-precision angular contact bearing pairs, pre-loaded and lubricated for life with
special grease for high speeds. When the machine is switched on for the first time every day, allow the
electrospindle to perform a brief preheating cycle in order to allow the bearings to gradually attain a uniform
operating temperature, and hence to obtain a uniform expansion of the bearing races and the correct
preload and rigidity.
The following cycle is recommended, without machining operations:
50 % of the maximum rated speed for 2 minutes.
75 % of the maximum rated speed for 2 minutes.
100 % of the maximum rated speed for 1 minute.
The preheating cycle should also be performed every time that the machine is inoperative long enough for
the electrospindle to cool down to room temperature.
TOOL HOLDER
ISO30 TOOL HOLDER
When you choose tool holders, you must consider the following conditions:
The cone geometry must conform to the DIN 69871.
The tool-holder cone ISO30 must have an AT3 precision rating.
Avoid the presence of plugs, slots, or other forms affecting the dynamic balancing of the toolholder;
At the maximum rated speed of the electrospindle, the level of dynamic balancing must be G =2.5 or
better (ISO1940 standard).
The balancing must be carried out with the tool-holder assembled (cone, mill collet, ring nut, tool);
Use only qualified tie-rod.
Install the tie rod in the ISO 30 cone in the following manner:
Carefully clean the tie-rod and the tie-rod housing in the cone ISO30.
Cover the thread of the tie-rod with high resistance, thread-blocking liquid (LOCTITE 270 or another
equivalent product).
Tighten the tie-rod to the cone with a torque of 62 Nm.
Leave the cone to rest, to allow the thread-blocking liquid to adhere (12 hours with LOCTITE 270, or
depending on the manufacturer's indications if using an alternative, equivalent threadblocker).
ISO cone
Tie-rod
26