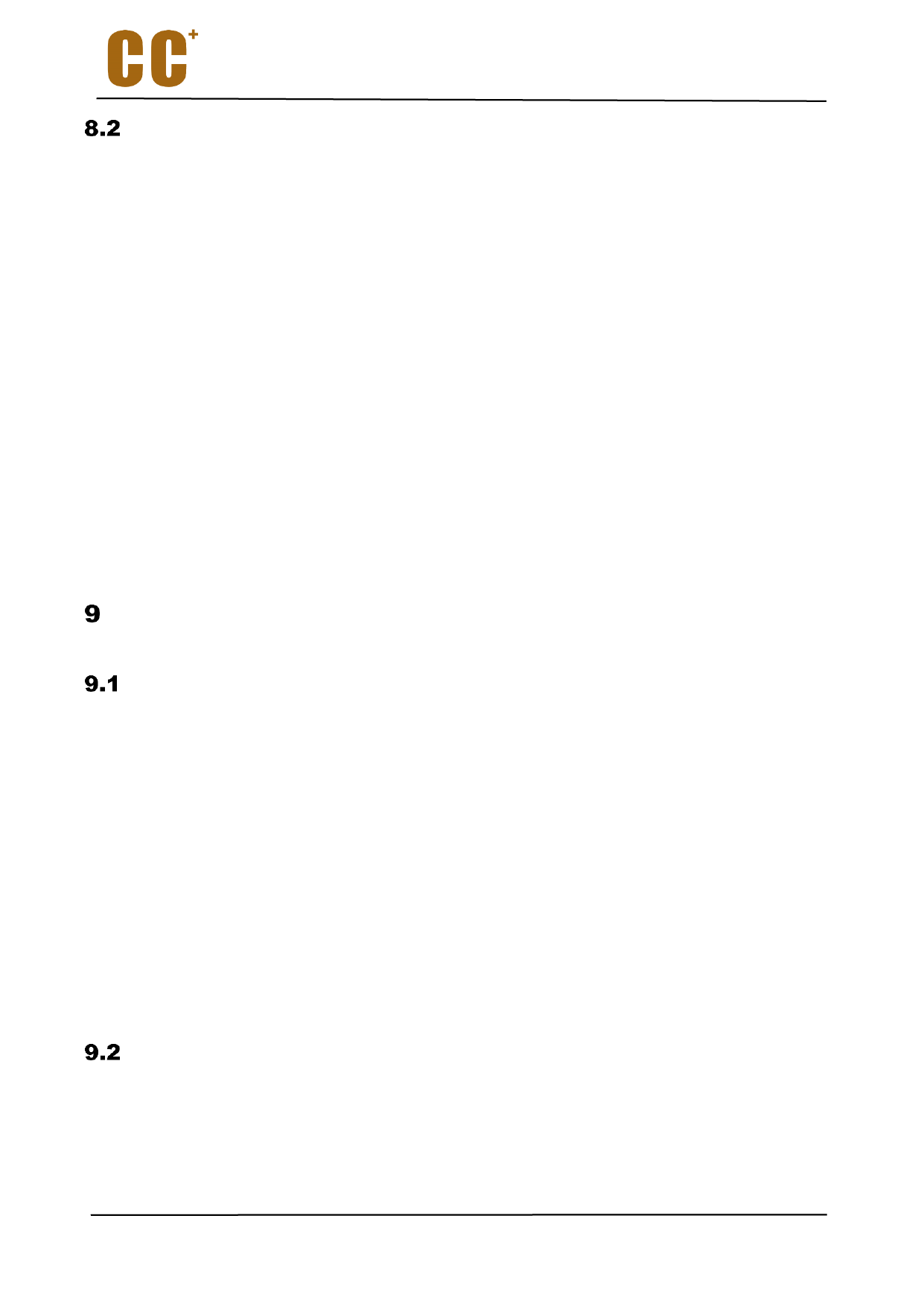
START-UP CHECKS.
Briefly run the electrospindle to warm up.
Ensure that the compressed air comes out from the front end of the electrospindle.
Compressed air should be provided at any time even when the electrospindle is not running.
Check the airflow from the fan to the nose end.
Even when the electrospindle is not running, the fan should be turned on.
Check the cone cleaning airflow when changing the tool.
Check the clearance (at least 1 mm) between the compressed air hose and the electrical cable or
machine parts.
Check whether the electrospindle control sensor meets the use requirements.
The tool holder must be ejected by 0.5-0.9mm when release the tool holder.
It is only when the electrospindle and the machine are standstill that the tool can be changed.
(The sensor 2 is on and the sensor 1 is off)
Button on the terminal box must be able to do manually tool change.
This button must only be used when the electrospindle and the machine are standstill.
The direction of the spindle rotation must comply with the setting of the digital controller.
USE AND ADJUSTMENT
ENVIRONMENTAL CONDITIONS
According to the Company's design and test, the electrospindle should work under the following
conditions:
The elevation is above sea level is less than1000m.
The maximum ambient air temperature does not exceed 40 ℃ (104 ℉)
The minimum ambient air temperature is higher than -15 ℃Celsius (5 ℉)
The coolant temperature at the entrance of the electrospindle (if there is) is between 23 ℃(73 ℉)
and 27 ℃ (81 ℉) .
In addition to the above limitations, there are other limitations in the table and figures of section 7.
If your specific working condition is not included in this manual, please contact the CCMOTOR to obtain
information about installation.
RUNNING-IN
Before being packed, the product was subjected to an automatic running-in cycle to guarantee the correct
distribution of the lubricant (long-life grease) on the races of the bearings, and to run in the spheres and
races of the bearings themselves. The running-in cycle also includes a strict inspection of all the command
and signaling elements, simulating various types of operating cycle on the test bench.
25